Regulations
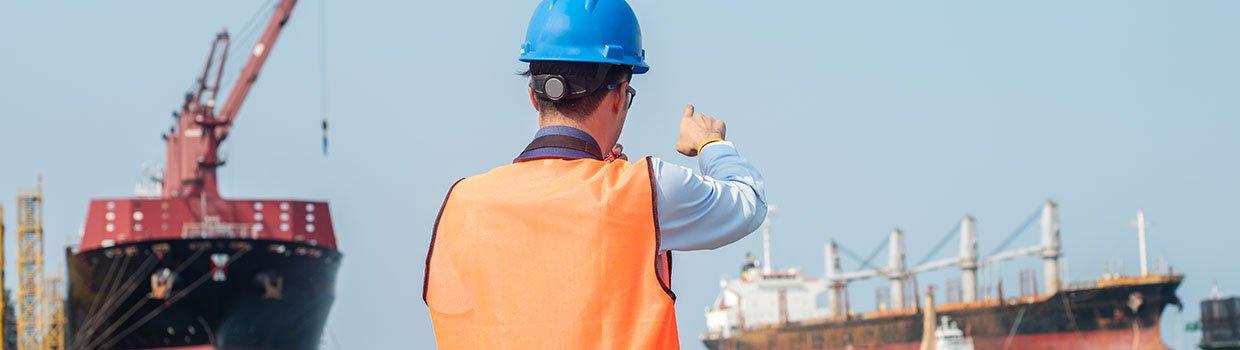
Inmarsat Maritime, a Viasat company, has announced Caribe Tankers USA, Inc (CTU) will trial Inmarsat’s fully managed bonded connectivity service, NexusWave, on board the chemical tankers Caribe Maria and Caribe Luna: as the US-based company seeks an ultra-reliable solution to best serve operational and crew connectivity. By combining multiple network underlays in one fully managed, bonded solution, Inmarsat’s NexusWave enables applications to leverage the aggregate capacity of all a...
In a landmark event, a meticulously reconstructed 5th-century wooden stitched ship was launched into the waters of the Mandovi River in Goa. This endeavour, a collaborative effort between the Ministry of Culture, the Indian Navy, and Hodi Innovations Pvt. Ltd., signifies a monumental step in reviving India's ancient maritime traditions. Modern stability and strength needs IRS has been instrumental in this project, ensuring that while the vessel retains its historical design Indian Register o...
The English Commercial Court (the “Court”) has provided helpful clarity on the extent of damages available to a claimant shipowner for the late redelivery of a vessel under a time charter where there is evidence that the owner of the vessel would have been unable to enter into a subsequent charter for the vessel. In such circumstances, only nominal damages will be recoverable, as no actual loss has been suffered. Background Hapag-Lloyd AG (the “Charterers”) entered i...
In recognition of its exceptional achievement in maintaining a safe work environment, the National Safety Council (NSC) presented ABS with two safety awards. The NSC is a globally recognised nonprofit organisation committed to eliminating leading causes of preventable death and injury in the workplace and on roadways. Their awards program recognises organisations and individuals who have made significant contributions to upholding the safety of their workplaces and communities. ABS’ acco...
On the occasion of its 50th Foundation Day on 4th April 2025, the Indian Register of Shipping (IRS) achieved a remarkable milestone by setting an Indian record for the ‘Largest Corporate Flag made on cloth’, as recognised by the India Book of Records. The massive flag, measuring 60 feet by 40 feet, was unfurled within the IRS Head Office premises. Adorned with the organisation’s logo, emblem, and corporate colours, the flag stands as a bold and symbolic representation of...
Transport Secretary, Heidi Alexander, said: “Today we mark significant progress in our journey to creating a greener, cleaner planet with a landmark agreement at the International Maritime Organization." “We have worked closely with international partners to forge a path for sustainable shipping internationally and secure a prosperous, resilient sector, laying a strong foundation for the future." Development of clean fuels Alexander added: “This deal means t...
News
Brunvoll has signed a contract with Rizhao Gangda Shipyard for the delivery of an extensive propulsion, manoeuvring, and dynamic positioning system for an Emergency Towing Vessel (ETV). The vessel is owned by Smit Lamnalco, a subsidiary of Boskalis, and will operate for the Austral Maritime Safety Authority. Its mission is to protect the marine environment around the Great Barrier Reef and Torres Strait – some of the most precious marine areas in the world. Brunvoll twin-screw propulsion system Brunvoll consists of the twin-screw propulsion system, 4 tunnel thrusters, and advanced control system The delivery from Brunvoll consists of the twin-screw propulsion system, four tunnel thrusters, and a highly advanced control system. “We are proud and humble for been chosen by such a major player in the maritime industry. The control system for this vessel is one of the most advanced systems to date by Brunvoll." "We have been working with this project for quite a while, and it is outer most rewarding when it finally comes together. All disciplines in Brunvoll have been working closely together with the owner and designer to realise this project, and even though the schedule is tight we will deliver on time,” says Oddbjørn Følsvik, VP Sales at Brunvoll. DP system features The control system delivery is one of the most advanced from Brunvoll to date. It includes Brunvoll’s Propulsion and Thruster Control system (BruCon PTC), Brunvoll’s Dynamic Positioning system (BruCon DP2), and Brunvoll’s Joystick control (BruCon JS). The DP system features Target Tracking, which allows the vessel to follow objects, such as Remotely Operated Vehicles (ROVs). Twin screw propulsion solution The propellers will have a maximum power output of 3800 kW each, and a diameter of 3.5 metres The twin screw propulsion solution consists of a pair of controllable pitch propellers with reduction gearboxes and nozzles. The propellers will have a maximum power output of 3800 kW each, and a diameter of 3.5 metres. The gearboxes also feature Power Take-Out (PTO) and Power Take-In (PTI), which allows for a broad variety of operational modes. All the different modes are available both in normal operation and while the vessel is in DP2 operation as well. Operational modes of the system The system will feature the following operational modes: PTO: Main engines and shaft generators running PTO on both sides, delivering both power for propulsion and electricity on board. PTI: Propulsion on both sides running by the electrical motors, powered either by auxiliary motors or batteries. In lower load conditions, this mode can be used to avoid starting up the larger main engine and instead run smaller engines on more optimal load conditions. Hybrid: One side runs PTO and the other runs PTI, i.e., one main engine powers both propellers. Adding further flexibility and optimal running of engines. Bollard pull: Both sides powered by main engines and PTI, for maximum bollard pull. This boost mode takes out the full power of the vessel to support special operations, like towing or anchor handling. Fire Fighting: FIFI pumps engaged with less power available for propulsion, to avoid overloading the main engine. The vessel was designed by Robert Allan Ltd. with the design annotation RASalvor 6500. The dimensions of the ETV are a length of 65 metres and a bollard pull capability of 120 tons.
Sentinel Marine, a member of the Cyan Renewables Group, has signed a shipbuilding contract with Jiangmen Hangtong Shipbuilding Co., Ltd for the construction of a 65-metre multi-role energy support vessel to join their fleet, with options for a further three vessels. The new vessel will bring the fleet number to 15. The initial vessel in this innovative new class is scheduled for delivery in Q2 2027. The newbuild will be a DP2 vessel with a deadweight of 1,600 tonnes, with 375m² of clear deck space and substantial under-deck capacity for fuel oil, potable water, recovered oil, and mono ethylene glycol (MEG). Dutch and Danish ERRV regulations Design includes an optional work-to-work gangway, an under-deck supplies storage and hybrid propulsion Designed as a Group B (A option) UK emergency response and rescue vessel (ERRV), the vessel will feature a fast rescue craft (FRC) and hybrid daughter craft. This transitional vessel will also meet design criteria for Dutch and Danish ERRV regulations and will offer accommodation for between 37 and 47 personnel. In addition to its emergency response capability, the design includes an optional work-to-work gangway, under-deck supplies warehouse and battery hybrid propulsion, ensuring suitability for a broad range of operations, including offshore wind and transitional energy support, government services, carbon capture, and maritime security. Innovation in marine operations Rory Deans, CEO of Sentinel Marine, says, "This new vessel, and the future sister ships, mark an exciting step forward in our strategic vision to deliver ‘Blue to Green' operations. The new vessel will be a cornerstone in our journey towards cleaner, multi-sector marine services that remain robust and reliable." Keng Lin Lee, CEO of Cyan Renewables, said: "Cyan is delighted to be investing in expanding our fleet with this innovative new multi-purpose support vessel enhancing Sentinel's reputation as the pioneering UK-based ERRV provider with the youngest fleet in Europe. The investment aligns with Sentinel Marine and Cyan Renewables' shared commitment to sustainable innovation in marine operations, strengthening the group's capabilities across multiple offshore sectors."
Fincantieri, a pioneer in complex shipbuilding, and Accenture, one of the world’s pioneering professional services companies, have signed an agreement to establish Fincantieri Ingenium, a new joint venture. The company will be owned 70% by Fincantieri NexTech – a subsidiary of the Fincantieri Group – and 30% by Accenture. The initiative stems from a Memorandum of Understanding signed in July 2024 and combines Fincantieri’s technological expertise in the naval sector with Accenture’s advanced digital capabilities and digital engineering and manufacturing expertise. The project is subject to customary regulatory clearances. Fincantieri Group’s Industrial Plan Fincantieri Ingenium has been created to accelerate digital transformation across the cruise industry Fincantieri Ingenium has been created to accelerate digital transformation across the cruise, defence, and port infrastructure sectors. It will play a key role in executing the strategy outlined in Fincantieri Group’s Industrial Plan. The goal is to enhance the offering of digital services and systems based on recent advances in technologies such as artificial intelligence by optimising the entire value chain through data utilisation and process transformation. Accenture’s extensive experience in digital platforms The joint venture will integrate Accenture’s extensive experience in digital platforms, AI, connectivity and IoT, cybersecurity, and service design with Fincantieri’s deep technological know-how in the naval and defense industries. This powerful combination will enable the development of new technological capabilities and skills, while also attracting and training new talent. Next-generation ships and existing fleets The first ship equipped with Navis Sapiens is expected to enter service by the end of 2025 Among the first strategic initiatives of the new company is the development of Navis Sapiens, a digital ecosystem designed for next-generation ships and the upgrade of existing fleets. The project spans three key dimensions: the creation of a portfolio of application services to optimise operational efficiency and lifecycle management for ships and onshore infrastructure; the development of a digital platform enabling these applications and advanced AI-driven functionalities, with a strong focus on cybersecurity; and a marketplace to facilitate the exchange of solutions - including those from third parties - to deliver high value-added services and enable new business models across the maritime ecosystem. The first ship equipped with Navis Sapiens is expected to enter service by the end of 2025. Ships and onshore ecosystems In synergy with Navis Sapiens, the joint venture also plans to enhance real-time data exchange and connectivity between ships and onshore ecosystems - including ports and shipyards - through a sea-to-shore interoperability solution to increase cross-functional process efficiency. This project will help improve the competitiveness of Italian ports by optimising performance across the entire maritime and land-based value chain. National maritime ecosystem The plans will be designed to reduce environmental impact via data-driven energy optimisation All initiatives will be promoted with sustainability as a core pillar. The systems will be designed to reduce environmental impact through data-driven energy optimisation, supporting shipowners in reducing fuel consumption. The initiatives already underway, as well as those to come, will generate significant value for Fincantieri, the national maritime ecosystem, and the country as a whole, with a positive impact on a global scale. Fincantieri technological innovation Pierroberto Folgiero, CEO and General Manager of Fincantieri, said: "With Fincantieri Ingenium, we strengthen our leadership position in technological innovation applied to shipbuilding and the naval engineering industry. This joint venture represents a strategic step forward in accelerating the digitalisation of the sector, leveraging artificial intelligence and the most advanced technologies." "Thanks to the synergy with Accenture, we will develop cutting-edge solutions that will make our ships and infrastructures increasingly connected, efficient and sustainable, consolidating Fincantieri's role as a pioneer in the sector." Step forward in maritime innovation Teodoro Lio, MU Lead for ICEG and CEO of Accenture Italy, commented: “We are excited about this joint venture with Fincantieri, which marks a significant step forward in maritime innovation and is a tangible example of collaboration between two organisations committed to transforming the market and creating new value." "With Fincantieri Ingenium, we are combining our respective strengths to shape new operating models that will transform maritime operations through innovative technologies.”
How to take the industry’s ‘ultimate planning tool’ and improve it? Giving users what they need, often before they know they need it, and staying ahead of evolving trends and regulations? Timo Essers, e-Navigation Director at NAVTOR, explains the philosophy driving the continual evolution of NavStation, while outlining the headline updates to the soon-to-be released NavStation 6.4. Navigators and shipping businesses "When you have products and services onboard over 18,000 vessels you tend to get a lot of feedback!" said Timo Essers may be grinning broadly, but he has a very serious point. The Dutch-born e-Navigation Chief at Norwegian-headquartered NAVTOR says he, and his global team, are committed to 'making life easier' for both navigators and shipping businesses, but to do that they have to understand current and future pain points. Maritime planning capabilities Partnership now pushing maritime planning abilities to new heights with the release of NavStation 6.4 "It’s not up to us to dictate to users, but rather to have them dictate to us – sharing their experience so we can use ours, both digital and navigational, to come up with optimal solutions," says Timo Essers, adding: "This industry is increasingly complex, with new regulations, guidelines, commercial considerations, reporting requirements, and risks emerging continually." He continues, "By putting the customer at the absolute centre of everything we do, and understanding their challenges, we can help them navigate this complexity simply, efficiently and profitably. In that way we’re not really a supplier – more of a partner. Always onboard to deliver added value, translating demands into innovations." It's a partnership currently pushing maritime planning capabilities to new heights with the upcoming release of NavStation 6.4. Transforming efficiency Launched in 2014 as the maritime industry’s first digital chart table, NavStation has spent the last decade cementing a position, in Essers’ words, as 'the ultimate planning tool'. Update after update has seen the software adding an increasing number of business- and operation-critical data layers and modules seamlessly over ENCs, putting 'everything a navigator needs at their fingertips'. The platform offers everything from weather routeing, to detailed port information, environmental regulations, AMVER reporting, a manoeuvring assistant, NAVAREA warnings, and much more, while automating tasks and auto-populating reports to slash administration, eradicate errors and enhance vessel and fleet efficiency. NavStation’s Passage Planning module NavStation’s popular Passage Planning module is a case in point, reducing time on each task NavStation’s popular Passage Planning module is a case in point, reducing time on each task from an average of 3.5 hours to 30 minutes, or less. “We may work in maritime technology, but the majority of the team here have extensive vessel experience,” says Essers, who is himself a seasoned navigation officer. “So, this is a platform made for navigators by navigators. We know the pressure our users are under. Thankfully, as we’ve shown with Passage Planning, we also know how to make things easier for them.” It's a process that, like the industry it serves, never stops. Small steps, big advantage Essers reveals that NavStation 6.4 sees a broad spectrum of enhancements, 'taking functionality and futureproofing to a new level.' In terms of functionality it has a vast range of 'small but powerful' improvements, he notes, including better search capabilities, advances in auto-routing (such as automatically blocking waterways for certain vessels based on the latest AIS tracking intelligence), integrating port and trade statistics into the extended ports database, the ability to combine company regulations with environmental regulations, and much more. NAVTOR’s ability to stay ahead of the curve and help customers navigate the future is shown in 6.4’s new S-100 compatibility. Enhancement of NavStation 6.4 The integration of real-time Security Risk Data from Risk Intelligence as a new, flexible subscription offering "Much of the industry may not be aware of the scale of change ahead with the upcoming S-100 data standard," states Timo Essers, adding "Transforming static charts into more dynamic, 3D, data-rich formats." He continues, "By making NavStation compatible, and giving users the ability to access data such as S-102 (bathymetric surface data) now, we can help them get to grips with this new navigational reality - understanding the benefits, honing skills, and easing future adoption. It’s a tangible example of how our approach delivers real added value." As is, arguably, the headline enhancement of NavStation 6.4, the integration of real-time Security Risk Data from Risk Intelligence as a new, flexible subscription offering. By the side worldwide “We’ve been working towards adding an up-to-the-minute risk layer over ENCs for some time,” Essers says, adding that it’s been, in his view, “a missing piece of the e-Navigation puzzle.” Now, however, that piece is firmly in place, allowing navigators, and relevant shore-side teams, to plan and understand voyages with safety and simplicity, fully aware of maritime’s ever-changing risk picture. Navigational jamming and spoofing Timo Essers explains: "From conflict and ongoing geopolitical unrest, to piracy, narcotics, and people smuggling - in addition to increasing navigational jamming and spoofing - today’s shipping companies face a complex and ever-evolving threat landscape. Navigators are, in many ways, on the front line, and as such are under immense pressure." He continues, "However, with clear, customisable and relevant notifications layered onto ENCs – empowered by Risk Intelligence’s world-pioneering team of expert analysts – our users can now approach planning with informed peace of mind. We see this as a landmark development for our own product, but also for the industry – enabling safer, simpler and smarter navigation in a changing world of threat." Privilege and passion Despite the major updates, level of innovation and ability to lead the way in e-Navigation, Timo Essers insists "We’re not there yet, there’s more to come. I’m incredibly proud of what we, in conjunction with our partners and customers worldwide, have achieved with NavStation. We are delivering on our promise of developing smart solutions that make life easier for shipping companies, benefiting the whole industry." He smiles, adding, "I’ve always said we want to voyage towards perfection. But, in an ever-changing industry, that means perfection is shifting all the time – it’s a moving target. Although this could be somewhat of a depressing realisation – you put your heart and soul into a project only to find it’s never actually completed – Essers’ sees through an entirely different lens." Navigator planning “I enjoy the voyage,” says Timo Essers, with a beam worthy of any navigator planning the optimal route ahead. He continues, "Shipping is dynamic, that’s what makes it so interesting, and innovating to match evolving customer demands is both a privilege and, I think I can speak for the whole team, a passion. So, I’m looking forward to plenty more feedback, and developments, in the years to come."
Thetius, the globally renowned specialist maritime technology research firm, has partnered with specialist marketing and communications agency - Wake Media to deliver a unique service offering to its clients. The partnership creates an integrated, end-to-end research and communications service built on Thetius’ renowned expertise in market intelligence and Wake Media’s proven track record in powerful multi-channel campaign strategy and execution. Thetius and Wake Media partnership Research options include wide reports and analyses of market and technology trends and innovation David Cocoracchio, Managing Director at Thetius, says, "The maritime industry is at a pivotal moment and the Thetius and Wake Media partnership is intended to equip companies with the information and assets they need to make good decisions." He adds, "With ever-evolving challenges around safety, decarbonisation, technology and economics, we aim to create positive change by providing data-driven insights that can be communicated to the widest possible audience." Deep market intelligence Andy Ford, Managing Director of Wake Media, says, "By blending deep market intelligence with compelling storytelling and world-class execution, this partnership enhances the ability to transform insights into action that resonates with target audiences and drives real engagement." The partnership is aimed at delivering research commissions of all sizes and scope combined with a tailor-made communications plan to suit all kinds of business and objectives, complete with detailed evaluation when concluded. Research options include comprehensive reports Research options include comprehensive reports and analyses of market and technology trends and innovation, while the communications services can deliver launch events, media relations and content across the whole marketing mix.
ClassNK has issued an approval in principle (AiP) for an Onboard Carbon Capture and Storage system (OCCS) developed by Mitsubishi Shipbuilding. The certification confirms its feasibility from regulatory and safety perspectives. Interest in CO2 capture the method from exhaust gases is growing alongside fuel conversion as part of efforts to reduce GHG emissions from ships. In response, the development of OCCS is progressing. Safety requirements for OCCS ClassNK will often strive to contribute to advanced decarbonisation initiatives via safety assessments To support the smooth development and introduction of related technologies, ClassNK has published the 'Guidelines for Shipboard CO2 Capture and Storage Systems' as a subset of the ClassNK Transition Support Services. This guideline outlines safety requirements for OCCS and its installation on ships. ClassNK reviewed the design of the system based on 'Guidelines for Shipboard CO2 Capture and Storage Systems'. Upon confirming compliance with the prescribed requirements, ClassNK issues an AiP. ClassNK will continually strive to contribute to advanced decarbonisation initiatives through safety assessments and more. Approval in Principle (AiP) At the initial stage of designing or before the specific target ship to be implemented is decided, the design is examined based on the existing regulations such as international conventions and ship classification rules, and an Approval in Principle (AiP) is issued as proof of conformity with requirements. It also prevents rework of regulatory aspects in the post-process, shortens the examination time at the time of class registration, and can be used as a technical basis for external appeal of the design status.
Brunvoll has signed a contract with Rizhao Gangda Shipyard for the delivery of an extensive propulsion, manoeuvring, and dynamic positioning system for an Emergency Towing Vessel (ETV). The vessel is owned by Smit Lamnalco, a subsidiary of Boskalis, and will operate for the Austral Maritime Safety Authority. Its mission is to protect the marine environment around the Great Barrier Reef and Torres Strait – some of the most precious marine areas in the world. Brunvoll twin-screw propulsion system Brunvoll consists of the twin-screw propulsion system, 4 tunnel thrusters, and advanced control system The delivery from Brunvoll consists of the twin-screw propulsion system, four tunnel thrusters, and a highly advanced control system. “We are proud and humble for been chosen by such a major player in the maritime industry. The control system for this vessel is one of the most advanced systems to date by Brunvoll." "We have been working with this project for quite a while, and it is outer most rewarding when it finally comes together. All disciplines in Brunvoll have been working closely together with the owner and designer to realise this project, and even though the schedule is tight we will deliver on time,” says Oddbjørn Følsvik, VP Sales at Brunvoll. DP system features The control system delivery is one of the most advanced from Brunvoll to date. It includes Brunvoll’s Propulsion and Thruster Control system (BruCon PTC), Brunvoll’s Dynamic Positioning system (BruCon DP2), and Brunvoll’s Joystick control (BruCon JS). The DP system features Target Tracking, which allows the vessel to follow objects, such as Remotely Operated Vehicles (ROVs). Twin screw propulsion solution The propellers will have a maximum power output of 3800 kW each, and a diameter of 3.5 metres The twin screw propulsion solution consists of a pair of controllable pitch propellers with reduction gearboxes and nozzles. The propellers will have a maximum power output of 3800 kW each, and a diameter of 3.5 metres. The gearboxes also feature Power Take-Out (PTO) and Power Take-In (PTI), which allows for a broad variety of operational modes. All the different modes are available both in normal operation and while the vessel is in DP2 operation as well. Operational modes of the system The system will feature the following operational modes: PTO: Main engines and shaft generators running PTO on both sides, delivering both power for propulsion and electricity on board. PTI: Propulsion on both sides running by the electrical motors, powered either by auxiliary motors or batteries. In lower load conditions, this mode can be used to avoid starting up the larger main engine and instead run smaller engines on more optimal load conditions. Hybrid: One side runs PTO and the other runs PTI, i.e., one main engine powers both propellers. Adding further flexibility and optimal running of engines. Bollard pull: Both sides powered by main engines and PTI, for maximum bollard pull. This boost mode takes out the full power of the vessel to support special operations, like towing or anchor handling. Fire Fighting: FIFI pumps engaged with less power available for propulsion, to avoid overloading the main engine. The vessel was designed by Robert Allan Ltd. with the design annotation RASalvor 6500. The dimensions of the ETV are a length of 65 metres and a bollard pull capability of 120 tons.
Sentinel Marine, a member of the Cyan Renewables Group, has signed a shipbuilding contract with Jiangmen Hangtong Shipbuilding Co., Ltd for the construction of a 65-metre multi-role energy support vessel to join their fleet, with options for a further three vessels. The new vessel will bring the fleet number to 15. The initial vessel in this innovative new class is scheduled for delivery in Q2 2027. The newbuild will be a DP2 vessel with a deadweight of 1,600 tonnes, with 375m² of clear deck space and substantial under-deck capacity for fuel oil, potable water, recovered oil, and mono ethylene glycol (MEG). Dutch and Danish ERRV regulations Design includes an optional work-to-work gangway, an under-deck supplies storage and hybrid propulsion Designed as a Group B (A option) UK emergency response and rescue vessel (ERRV), the vessel will feature a fast rescue craft (FRC) and hybrid daughter craft. This transitional vessel will also meet design criteria for Dutch and Danish ERRV regulations and will offer accommodation for between 37 and 47 personnel. In addition to its emergency response capability, the design includes an optional work-to-work gangway, under-deck supplies warehouse and battery hybrid propulsion, ensuring suitability for a broad range of operations, including offshore wind and transitional energy support, government services, carbon capture, and maritime security. Innovation in marine operations Rory Deans, CEO of Sentinel Marine, says, "This new vessel, and the future sister ships, mark an exciting step forward in our strategic vision to deliver ‘Blue to Green' operations. The new vessel will be a cornerstone in our journey towards cleaner, multi-sector marine services that remain robust and reliable." Keng Lin Lee, CEO of Cyan Renewables, said: "Cyan is delighted to be investing in expanding our fleet with this innovative new multi-purpose support vessel enhancing Sentinel's reputation as the pioneering UK-based ERRV provider with the youngest fleet in Europe. The investment aligns with Sentinel Marine and Cyan Renewables' shared commitment to sustainable innovation in marine operations, strengthening the group's capabilities across multiple offshore sectors."
Fincantieri, a pioneer in complex shipbuilding, and Accenture, one of the world’s pioneering professional services companies, have signed an agreement to establish Fincantieri Ingenium, a new joint venture. The company will be owned 70% by Fincantieri NexTech – a subsidiary of the Fincantieri Group – and 30% by Accenture. The initiative stems from a Memorandum of Understanding signed in July 2024 and combines Fincantieri’s technological expertise in the naval sector with Accenture’s advanced digital capabilities and digital engineering and manufacturing expertise. The project is subject to customary regulatory clearances. Fincantieri Group’s Industrial Plan Fincantieri Ingenium has been created to accelerate digital transformation across the cruise industry Fincantieri Ingenium has been created to accelerate digital transformation across the cruise, defence, and port infrastructure sectors. It will play a key role in executing the strategy outlined in Fincantieri Group’s Industrial Plan. The goal is to enhance the offering of digital services and systems based on recent advances in technologies such as artificial intelligence by optimising the entire value chain through data utilisation and process transformation. Accenture’s extensive experience in digital platforms The joint venture will integrate Accenture’s extensive experience in digital platforms, AI, connectivity and IoT, cybersecurity, and service design with Fincantieri’s deep technological know-how in the naval and defense industries. This powerful combination will enable the development of new technological capabilities and skills, while also attracting and training new talent. Next-generation ships and existing fleets The first ship equipped with Navis Sapiens is expected to enter service by the end of 2025 Among the first strategic initiatives of the new company is the development of Navis Sapiens, a digital ecosystem designed for next-generation ships and the upgrade of existing fleets. The project spans three key dimensions: the creation of a portfolio of application services to optimise operational efficiency and lifecycle management for ships and onshore infrastructure; the development of a digital platform enabling these applications and advanced AI-driven functionalities, with a strong focus on cybersecurity; and a marketplace to facilitate the exchange of solutions - including those from third parties - to deliver high value-added services and enable new business models across the maritime ecosystem. The first ship equipped with Navis Sapiens is expected to enter service by the end of 2025. Ships and onshore ecosystems In synergy with Navis Sapiens, the joint venture also plans to enhance real-time data exchange and connectivity between ships and onshore ecosystems - including ports and shipyards - through a sea-to-shore interoperability solution to increase cross-functional process efficiency. This project will help improve the competitiveness of Italian ports by optimising performance across the entire maritime and land-based value chain. National maritime ecosystem The plans will be designed to reduce environmental impact via data-driven energy optimisation All initiatives will be promoted with sustainability as a core pillar. The systems will be designed to reduce environmental impact through data-driven energy optimisation, supporting shipowners in reducing fuel consumption. The initiatives already underway, as well as those to come, will generate significant value for Fincantieri, the national maritime ecosystem, and the country as a whole, with a positive impact on a global scale. Fincantieri technological innovation Pierroberto Folgiero, CEO and General Manager of Fincantieri, said: "With Fincantieri Ingenium, we strengthen our leadership position in technological innovation applied to shipbuilding and the naval engineering industry. This joint venture represents a strategic step forward in accelerating the digitalisation of the sector, leveraging artificial intelligence and the most advanced technologies." "Thanks to the synergy with Accenture, we will develop cutting-edge solutions that will make our ships and infrastructures increasingly connected, efficient and sustainable, consolidating Fincantieri's role as a pioneer in the sector." Step forward in maritime innovation Teodoro Lio, MU Lead for ICEG and CEO of Accenture Italy, commented: “We are excited about this joint venture with Fincantieri, which marks a significant step forward in maritime innovation and is a tangible example of collaboration between two organisations committed to transforming the market and creating new value." "With Fincantieri Ingenium, we are combining our respective strengths to shape new operating models that will transform maritime operations through innovative technologies.”
How to take the industry’s ‘ultimate planning tool’ and improve it? Giving users what they need, often before they know they need it, and staying ahead of evolving trends and regulations? Timo Essers, e-Navigation Director at NAVTOR, explains the philosophy driving the continual evolution of NavStation, while outlining the headline updates to the soon-to-be released NavStation 6.4. Navigators and shipping businesses "When you have products and services onboard over 18,000 vessels you tend to get a lot of feedback!" said Timo Essers may be grinning broadly, but he has a very serious point. The Dutch-born e-Navigation Chief at Norwegian-headquartered NAVTOR says he, and his global team, are committed to 'making life easier' for both navigators and shipping businesses, but to do that they have to understand current and future pain points. Maritime planning capabilities Partnership now pushing maritime planning abilities to new heights with the release of NavStation 6.4 "It’s not up to us to dictate to users, but rather to have them dictate to us – sharing their experience so we can use ours, both digital and navigational, to come up with optimal solutions," says Timo Essers, adding: "This industry is increasingly complex, with new regulations, guidelines, commercial considerations, reporting requirements, and risks emerging continually." He continues, "By putting the customer at the absolute centre of everything we do, and understanding their challenges, we can help them navigate this complexity simply, efficiently and profitably. In that way we’re not really a supplier – more of a partner. Always onboard to deliver added value, translating demands into innovations." It's a partnership currently pushing maritime planning capabilities to new heights with the upcoming release of NavStation 6.4. Transforming efficiency Launched in 2014 as the maritime industry’s first digital chart table, NavStation has spent the last decade cementing a position, in Essers’ words, as 'the ultimate planning tool'. Update after update has seen the software adding an increasing number of business- and operation-critical data layers and modules seamlessly over ENCs, putting 'everything a navigator needs at their fingertips'. The platform offers everything from weather routeing, to detailed port information, environmental regulations, AMVER reporting, a manoeuvring assistant, NAVAREA warnings, and much more, while automating tasks and auto-populating reports to slash administration, eradicate errors and enhance vessel and fleet efficiency. NavStation’s Passage Planning module NavStation’s popular Passage Planning module is a case in point, reducing time on each task NavStation’s popular Passage Planning module is a case in point, reducing time on each task from an average of 3.5 hours to 30 minutes, or less. “We may work in maritime technology, but the majority of the team here have extensive vessel experience,” says Essers, who is himself a seasoned navigation officer. “So, this is a platform made for navigators by navigators. We know the pressure our users are under. Thankfully, as we’ve shown with Passage Planning, we also know how to make things easier for them.” It's a process that, like the industry it serves, never stops. Small steps, big advantage Essers reveals that NavStation 6.4 sees a broad spectrum of enhancements, 'taking functionality and futureproofing to a new level.' In terms of functionality it has a vast range of 'small but powerful' improvements, he notes, including better search capabilities, advances in auto-routing (such as automatically blocking waterways for certain vessels based on the latest AIS tracking intelligence), integrating port and trade statistics into the extended ports database, the ability to combine company regulations with environmental regulations, and much more. NAVTOR’s ability to stay ahead of the curve and help customers navigate the future is shown in 6.4’s new S-100 compatibility. Enhancement of NavStation 6.4 The integration of real-time Security Risk Data from Risk Intelligence as a new, flexible subscription offering "Much of the industry may not be aware of the scale of change ahead with the upcoming S-100 data standard," states Timo Essers, adding "Transforming static charts into more dynamic, 3D, data-rich formats." He continues, "By making NavStation compatible, and giving users the ability to access data such as S-102 (bathymetric surface data) now, we can help them get to grips with this new navigational reality - understanding the benefits, honing skills, and easing future adoption. It’s a tangible example of how our approach delivers real added value." As is, arguably, the headline enhancement of NavStation 6.4, the integration of real-time Security Risk Data from Risk Intelligence as a new, flexible subscription offering. By the side worldwide “We’ve been working towards adding an up-to-the-minute risk layer over ENCs for some time,” Essers says, adding that it’s been, in his view, “a missing piece of the e-Navigation puzzle.” Now, however, that piece is firmly in place, allowing navigators, and relevant shore-side teams, to plan and understand voyages with safety and simplicity, fully aware of maritime’s ever-changing risk picture. Navigational jamming and spoofing Timo Essers explains: "From conflict and ongoing geopolitical unrest, to piracy, narcotics, and people smuggling - in addition to increasing navigational jamming and spoofing - today’s shipping companies face a complex and ever-evolving threat landscape. Navigators are, in many ways, on the front line, and as such are under immense pressure." He continues, "However, with clear, customisable and relevant notifications layered onto ENCs – empowered by Risk Intelligence’s world-pioneering team of expert analysts – our users can now approach planning with informed peace of mind. We see this as a landmark development for our own product, but also for the industry – enabling safer, simpler and smarter navigation in a changing world of threat." Privilege and passion Despite the major updates, level of innovation and ability to lead the way in e-Navigation, Timo Essers insists "We’re not there yet, there’s more to come. I’m incredibly proud of what we, in conjunction with our partners and customers worldwide, have achieved with NavStation. We are delivering on our promise of developing smart solutions that make life easier for shipping companies, benefiting the whole industry." He smiles, adding, "I’ve always said we want to voyage towards perfection. But, in an ever-changing industry, that means perfection is shifting all the time – it’s a moving target. Although this could be somewhat of a depressing realisation – you put your heart and soul into a project only to find it’s never actually completed – Essers’ sees through an entirely different lens." Navigator planning “I enjoy the voyage,” says Timo Essers, with a beam worthy of any navigator planning the optimal route ahead. He continues, "Shipping is dynamic, that’s what makes it so interesting, and innovating to match evolving customer demands is both a privilege and, I think I can speak for the whole team, a passion. So, I’m looking forward to plenty more feedback, and developments, in the years to come."
Thetius, the globally renowned specialist maritime technology research firm, has partnered with specialist marketing and communications agency - Wake Media to deliver a unique service offering to its clients. The partnership creates an integrated, end-to-end research and communications service built on Thetius’ renowned expertise in market intelligence and Wake Media’s proven track record in powerful multi-channel campaign strategy and execution. Thetius and Wake Media partnership Research options include wide reports and analyses of market and technology trends and innovation David Cocoracchio, Managing Director at Thetius, says, "The maritime industry is at a pivotal moment and the Thetius and Wake Media partnership is intended to equip companies with the information and assets they need to make good decisions." He adds, "With ever-evolving challenges around safety, decarbonisation, technology and economics, we aim to create positive change by providing data-driven insights that can be communicated to the widest possible audience." Deep market intelligence Andy Ford, Managing Director of Wake Media, says, "By blending deep market intelligence with compelling storytelling and world-class execution, this partnership enhances the ability to transform insights into action that resonates with target audiences and drives real engagement." The partnership is aimed at delivering research commissions of all sizes and scope combined with a tailor-made communications plan to suit all kinds of business and objectives, complete with detailed evaluation when concluded. Research options include comprehensive reports Research options include comprehensive reports and analyses of market and technology trends and innovation, while the communications services can deliver launch events, media relations and content across the whole marketing mix.
ClassNK has issued an approval in principle (AiP) for an Onboard Carbon Capture and Storage system (OCCS) developed by Mitsubishi Shipbuilding. The certification confirms its feasibility from regulatory and safety perspectives. Interest in CO2 capture the method from exhaust gases is growing alongside fuel conversion as part of efforts to reduce GHG emissions from ships. In response, the development of OCCS is progressing. Safety requirements for OCCS ClassNK will often strive to contribute to advanced decarbonisation initiatives via safety assessments To support the smooth development and introduction of related technologies, ClassNK has published the 'Guidelines for Shipboard CO2 Capture and Storage Systems' as a subset of the ClassNK Transition Support Services. This guideline outlines safety requirements for OCCS and its installation on ships. ClassNK reviewed the design of the system based on 'Guidelines for Shipboard CO2 Capture and Storage Systems'. Upon confirming compliance with the prescribed requirements, ClassNK issues an AiP. ClassNK will continually strive to contribute to advanced decarbonisation initiatives through safety assessments and more. Approval in Principle (AiP) At the initial stage of designing or before the specific target ship to be implemented is decided, the design is examined based on the existing regulations such as international conventions and ship classification rules, and an Approval in Principle (AiP) is issued as proof of conformity with requirements. It also prevents rework of regulatory aspects in the post-process, shortens the examination time at the time of class registration, and can be used as a technical basis for external appeal of the design status.


Expert commentary
When the Ballast Water Management (BWM) Convention came into force in 2004, it was in response to a crisis we couldn’t afford to ignore—one where invasive aquatic species, carried silently in ships’ ballast tanks, were devastating marine ecosystems. Now, two decades later, compliance with this environmental safeguard is no longer optional—and yet, as recent industry findings reveal, record-keeping failures account for 58% of compliance issues. That’s not a technology problem. That’s a documentation problem —one rooted deeply in data management practices and crew training, where small oversights lead to documentation issues, that may cascade into costly compliance failures. And that’s precisely where digital systems excel, guiding crews clearly to avoid mistakes in the first place. New ballast regulations At the IMO’s 82nd Marine Environment Protection Committee (MEPC 82), new ballast water record-keeping regulations were approved, coming into effect from 1 February 2025. These updates mark a significant tightening of documentation standards—and they could catch unprepared shipowners off guard if not acted on promptly. Why ballast water record-keeping is back in the spotlight These new updates aim to change that—and they’re stricter, smarter, and more detailed than before While MEPC 82 made headlines for advancing decarbonisation policies and ECAs in the Arctic and Norwegian Sea, it also honed in on ballast water—a topic that has quietly regained importance. The committee approved critical updates to how ballast water operations and ballast water management system (BWMS) maintenance are recorded. The goal: Enhance transparency, reduce ambiguity, and reinforce environmental protection by making records more structured, traceable, and actionable. This renewed focus is both a warning and an opportunity. In recent years, too many Port State Control detentions and inspection delays have stemmed not from hardware failures, but from poorly maintained or unclear ballast water records. These new updates aim to change that—and they’re stricter, smarter, and more detailed than before. What’s changing: Bypass scenarios and maintenance logging The revised guidelines introduce two new scenarios for vessels dealing with challenging water quality (CWQ) in ports: Scenario 3: A reactive bypass of the BWMS due to unforeseen poor water quality. Scenario 4: A pre-emptive bypass based on anticipated CWQ conditions. These additions are essential for vessels operating globally, particularly those above 400GT. They ensure that alternative operations—like ballast water exchange plus treatment (BWE + BWT)—are clearly documented. Without accurate records, even legitimate actions can fall short of compliance. Ballast Water Management Plan and OEM manuals MEPC 82 also mandates that BWMS care procedures must now be recorded directly in BWRB MEPC 82 also mandates that BWMS maintenance procedures must now be recorded directly in the Ballast Water Record Book (BWRB), in line with the ship’s Ballast Water Management Plan and Original Equipment Manufacturer (OEM) manuals. Responsible crew members must sign off on these records, ensuring traceability and crew accountability. This step isn’t just regulatory housekeeping—it aligns ballast water maintenance with how other onboard systems are already tracked, from engines to emissions. It’s a logical, overdue move toward consistency across compliance. Paper or digital: The format dilemma While the BWRB can still be maintained on paper or electronically, the burden of new structured data fields and stricter reporting timelines will be felt most by those still tied to manual systems. Each additional layer of documentation increases the chance of human error—and with nearly 6 in 10 compliance failures already stemming from admin issues, that’s a risk many operators can’t afford. This is where digital solutions can offer real relief. At NAPA, we’ve already implemented the latest IMO guidelines into our electronic logbook, so crews can comply with MEPC.369(80) requirements out of the box. With ready-made entry templates and smart input validation, data entry is quick, accurate, and audit-ready. NAPA implemented the latest IMO guidelines into an electronic logbook. Better still, once updated, operators can apply for the BWM Convention Electronic Record Book Declaration from their flag—ensuring that compliance is recognised internationally under MEPC.372(80). Less admin, more assurance Electronic logbooks don’t just streamline compliance—they enable better decision-making. When connected to onboard systems, they automatically pull operational data into the BWRB, reducing manual work and error margins. This frees up the crew to focus on operations and safety, rather than paperwork. From a management perspective, real-time visibility into ballast operations and maintenance records helps shore teams stay ahead of inspections and identify potential compliance gaps early. One logbook, many regulations While ballast water is the focus today, it’s not the only regulation demanding attention While ballast water is the focus today, it’s not the only regulation demanding attention. At NAPA, we’ve designed our logbook to support a wide range of evolving compliance frameworks—including MARPOL, EU-ETS, EU-MRV, CII, and the Garbage Record Book. This unified approach removes silos, reduces duplicated effort, and gives operators a more holistic view of vessel performance and compliance. A smarter way forward With decarbonisation and environmental regulations shifting at breakneck pace, even the most experienced crews and fleet managers can struggle to stay up to date. That’s where technology has a crucial role to play—not to replace expertise, but to support it. At NAPA, we work closely with shipowners and operators to configure regulatory record book templates according to their fleet workflows and each vessel’s specific operational profile. This ensures accuracy, ease of use, and most importantly, continuous compliance—even as the rules keep changing. Because in today’s compliance landscape, staying ahead isn’t just about meeting the minimum. It’s about building systems that help you adapt, respond, and thrive. And that starts with getting the record-keeping and data management right.
President Donald Trump has already made plenty of headlines since taking up his second term in the White House, including with the announcement of numerous new tariffs on imports. The 47th United States President issued three executive orders on February 1st 2025, just days after his inauguration, which directed the US to impose an additional 25 percent ad valorem rate of duty on imports from Canada and Mexico, as well as ten percent on imports from China. How Trump’s 2nd term as US President Cleveland Containers has analysed the early reactions to these announcements Excluding Canadian energy resources exports – which instead will be hit with a ten percent tariff – the tariffs have been applied to all imports which are either entered for consumption or withdrawn from warehouse for consumption on or after 12:01 am Eastern Standard Time on February 4th 2025. President Trump also told reporters on February 8th 2025 that a 25 percent tariff on all American steel and aluminium imports was coming into effect across the US during February. Leading 40ft shipping container supplier Cleveland Containers has analysed the early reactions to these announcements and how President Trump’s second term as US President could affect the world’s shipping industry, especially when looking back at his first term. Reaction to President Trump’s tariff announcements Mexico, Canada and China were all quick to react to President Trump’s announcement of tariffs on imports. Mexican President Claudia Sheinbaum said her country would vow for resilience against the measures, while a senior government official in Canada said that their country would challenge the decision by taking legal action through the necessary international bodies. China has also said it would be challenging the tariffs at the World Trade Organisation. According to the country’s finance ministry, as reported on by Geopolitical Intelligence Services, Beijing were moving to place levies of 15 percent on American coal and liquefied natural gas, as well as levies of ten percent on crude oil, certain vehicles and farm equipment. Beginning of making America rich again When it comes to the announcement of the tariff on all American steel and aluminium imports, President Trump told reporters in the Oval Office: "This is a big deal, the beginning of making America rich again. Our nation requires steel and aluminium to be made in America, not in foreign lands.” Francois-Phillippe Champagne, the Minister of Innovation in Canada, stated that the tariffs were "totally unjustified" though, before adding in a post on X: "Canadian steel and aluminium support key industries in the US, from defence, shipbuilding and auto. We will continue to stand up for Canada, our workers, and our industries." How might President Trump’s 2nd term affect shipping sector? Bruce Chan, an analyst in the Transportation and Future Mobility sectors at wealth management and investment banking Just ahead of President Trump taking office for the second time, J. Bruce Chan, an analyst in the Transportation and Future Mobility sectors at wealth management and investment banking firm Stifel, believed that the shipping industry was prepared for the new tariffs. However, he also stated to the Morning Star: "President Trump's Administration promises to usher in a new trade and tariff regime. As such, it's difficult to assess the ultimate impact to the freight transportation industry. Prima facie, we believe tariffs are a drag on freight demand, effectively resulting in higher costs for shippers that are generally passed on to end consumers over time." Attention to the American sanction announcements Mr. Chan went on to note that those involved in shipping containers across continents should be paying particular attention to the American sanction announcements. He commented: "Because almost all trans-Pacific trade moves over the ocean, we believe ocean container shipping will see the largest direct impact. But for shippers and retailers, there is no cheaper way to move goods than over the ocean, so there are few modal alternatives if production remains in Asia. We see the most risk for maritime shipping, with containers and dry bulk being more acute, with more insulation for oil and gas tankers." Shipping news and intelligence service Various sources have looked back on President Trump’s first term to get an idea of what could be expected As President Trump has just become his second term as US president and the American sanctions have only just been announced, it will take time to see what the true impact will be. However, various sources have looked back on President Trump’s first term to get an idea of what could be expected. For example, shipping news and intelligence service Lloyd’s List pointed out that tariffs introduced when President Trump was last in the White House had a noticeable effect on both spot container freight rates and import timing. Cargoes were pulled forward in the second half of 2018 by importers as they looked to beat tariff deadlines, which resulted in higher spot rates temporarily before affecting rates in 2019 because of inventory overhang. Could repeat results be seen across 2025 and 2026? Long-life inputs and goods from the tariff countries Jason Miller, a freight economist and professor of supply chain management at Michigan State University, certainly seemed to think so. Speaking to Lloyd’s List before President Trump’s 2024 presidential victory when the tariffs were only part of campaign proposals at that point, he said: “We will see front-loading like we have never seen before in 2025. There would be a massive pull-forward of demand as everybody rushes to bring in long-life inputs and goods from tariff countries, especially China.” Shipping demand and routes Shipping demand and routes could be affected due to trade uncertainty too Meanwhile, international shipping and forwarding agents Supreme Freight Services reported that increased tariffs may cause disruption to shipping volumes and global supply chains, if trade policies introduced by President Trump during his first term are anything to go by. Shipping demand and routes could be affected due to trade uncertainty too, though the publication also acknowledged that increased investment in ports and inland waterways across the US could improve efficiency for domestic and international trade alike. New American sanctions Cleveland Containers has looked to reassure its customers that any disruption caused by the new American sanctions will be minimised at the firm. Hayley Hedley, the company’s Commercial Director, stated: “Recent history certainly suggests that the new tariffs being introduced by President Trump will have various knock-on effects across the shipping industry." “Fortunately, Cleveland Containers has a continuous supply of shipping containers entering the UK. We work with several agents to ship from various locations, as well as having good stock on the ground, so are confident in our ability to provide for our customers.”
The shipping industry is currently navigating a profound transformation driven by environmental concerns, new emissions targets, and evolving regulations. As vessel owners and operators seek to reduce emissions while remaining competitive, determining the right strategy has become increasingly complex. Factors such as alternative fuel availability, fluctuating prices, and an ever-expanding range of technological solutions have made decision-making anything but straightforward. Lack of motivation Regulations evolve, technologies persist to advance, and can differ greatly from port to port The complexity arises from the many moving parts of the industry. Regulations evolve, technologies continue to advance, and infrastructure can differ greatly from port to port. For vessel owners committed to reducing their environmental impact, the challenge isn’t a lack of motivation, it’s finding the most effective way to navigate the myriad of options available. Hybrid propulsion systems One method gaining traction is data-driven decision-making through digital modelling. Rather than making decisions based on guesswork, digital modelling allows owners and operators to create a detailed representation of a vessel and simulate the performance of different strategies or technologies over its lifetime. That way, they can ‘test’ these approaches before committing large investments—particularly useful when considering new fuels or hybrid propulsion systems that are still maturing. Decarbonisation Modelling Service Digital modelling accounts for variables such as vessel speed, power needs, and route patterns Digital modelling accounts for variables such as vessel speed, power needs, and route patterns, applying machine-learning algorithms to find the most promising design or retrofit. It can also show how ideas might evolve if regulations tighten, or new fuels become more practical. At Wärtsilä, our Decarbonisation Modelling Service is designed to guide shipowners and operators through this maze of choices. In developing this tool, we have observed that shipowners required more than an “off-the-shelf” solution. They needed insights based on their own operational data, combined with practical knowledge of costs and likely regulatory trends. Benefits of digital modelling One of the main benefits of digital modelling is its flexibility. Depending on an owner’s goals, whether that’s meeting today’s regulations or planning for future mandates, they can explore multiple options. A fleet operator might compare installing hybrid batteries versus retrofitting for LNG or consider alternative fuels such as ammonia and methanol, or carbon capture. These simulations can factor in fuel prices, available bunkering infrastructure, and even unexpected events like global supply chain disruptions or future carbon taxes. Ship’s actual operational profile At Wärtsilä we often liken digital modelling as the closest thing to a crystal ball At Wärtsilä we often liken digital modelling as the closest thing to a crystal ball. While it isn’t perfect, it significantly improves our ability to make informed decisions and maintain flexibility as market conditions or regulatory landscapes shift. Consider, for instance, a mid-sized container ship operating in Asia. The owner, eager to lower CO2 emissions, might be unsure whether to retrofit for LNG immediately or wait for ammonia infrastructure to mature. Using a digital model based on the ship’s actual operational profile, we can test both scenarios—evaluating fuel price trends, port facilities, and the vessel’s remaining service life. Adopt an interim strategy If the model indicates that an LNG retrofit offers a promising return on investment along with moderate emissions cuts, the decision becomes clearer. Alternatively, if the potential for ammonia becomes evident sooner, it might be wiser to adopt an interim strategy or consider dual-fuel engines. It’s important to recognise that decarbonisation is not merely a box-ticking exercise to meet current regulations; it is a dynamic, ongoing process. With tightening rules from bodies like the International Maritime Organization (IMO) and the EU on carbon intensity, and with cargo owners increasingly demanding transparency, the need for adaptive, data-driven solutions is more critical than ever. LNG with battery storage Others might make quick retrofits to comply with rules and plan for bigger upgrades later Another strength of data-driven decarbonisation is that it is not a one-off activity. As a vessel operates, new information becomes available. Owners can update their models to reflect these shifts, allowing for continuous refinement. This matters because what is optimal now may only be a temporary measure. Some operators use LNG with battery storage for a few years, then switch to next-generation fuels as they become viable. Others might make quick retrofits to comply with regulations and plan for bigger upgrades later. Raw data into actionable insights There is also a perception that gathering and interpreting data is too complex or costly. However, many modern vessels are already equipped with the necessary sensors and tracking systems, and analytics software has become more accessible. The real value lies in transforming raw data into actionable insights. Digital models not only help in planning for evolving market conditions but also enable us to visualise and execute long-term strategies. Portion of global CO2 emissions The real test is balancing environmental aims with retail realities and regulatory forces Shipping contributes a notable portion of global CO2 emissions, giving the industry strong financial and ethical reasons to embrace cleaner operations. The real test is balancing environmental aims with commercial realities and regulatory pressures. With mounting pressure from regulators, customers, and investors, now is an opportune time to adopt data-driven approaches. A continuously updated model provides a practical way to keep up with changes in the market and policy landscape. By integrating operational data, anticipating possible scenarios, and remaining open to new solutions, the maritime industry can cut emissions without sacrificing competitiveness. Shipowners and operators Shipping is an industry that operates on tight margins and these tools must deliver financial stability as well as ongoing compliance. Digital modelling is not just another technical tool; it’s a forward-looking process that helps shipowners and operators steer a confident course in uncertain waters. As more companies experiment with alternative fuels, hybrid propulsion, and emerging technologies, having a robust method for evaluating these options is absolutely essential.
Harbour insights
Ammonia is gaining traction as a future fuel in the maritime industry, primarily due to its potential to significantly reduce greenhouse gas emissions. A key driver for ammonia's interest is that it can be carbon-free when combusted, which aligns with the maritime industry's increasing pressure to meet emissions regulations. However, most ammonia production currently relies on fossil fuels. Transitioning to "green ammonia" production is crucial for sustainability. If "green ammonia" is produced using renewable energy sources, it offers a pathway to near-zero emissions shipping. Safety measures and regulations Ammonia’s volumetric energy density – higher than hydrogen – makes it more practical for onboard storage. However, ammonia is toxic, which requires stringent safety measures and regulations for handling and storage. The combustion of ammonia can produce nitrous oxide (N2O), a potent greenhouse gas. Therefore, mitigation technologies are needed. Building the necessary infrastructure for ammonia bunkering and supply will be a significant undertaking. Developing guidelines for safe use Ammonia is poised to play a significant role in the maritime industry's transition to a future The International Maritime Organization (IMO) is developing guidelines for the safe use of ammonia as a marine fuel. Increasing numbers of companies are investing in the development of ammonia-fueled vessels and technologies. European Union (EU) legislation, such as the EU Emissions Trading System (ETS) and the FuelEU initiative to support decarbonisation, are pushing the maritime industry towards the use of alternative fuels, which is increasing the potential of ammonia. While challenges remain, ammonia is poised to play a significant role in the maritime industry's transition to a more sustainable future. Ongoing research and development Ongoing research and development are focused on improving safety, reducing emissions, and scaling up production. In essence, ammonia offers a promising pathway for the maritime industry to reduce its carbon footprint, but its widespread adoption depends on overcoming technical and logistical challenges. Working toward the future of ammonia Progress is already happening as the maritime industry works toward a future that includes the use of ammonia as a fuel. For example, one project underway aims to be a pioneer in establishing a comprehensive and competitive supply chain to provide clean ammonia ship-to-ship bunkering in the U.S. West Coast. Progress is already occurring as the maritime industry works toward a future A feasibility study is being conducted at the Port of Oakland, Benicia, and nearby major ports on the U.S. West Coast. A Memorandum of Understanding (MOU) between American Bureau of Shipping, CALAMCO, Fleet Management Limited, Sumitomo Corp. and TOTE Services LLC is jointly conducting the feasibility study. "We are proud to share our industry-pioneering expertise in ammonia as a marine fuel to support this study on the U.S. West Coast,” said Panos Koutsourakis, Vice President of Global Sustainability at the American Bureau of Shipping. “Our expertise in developing safety guidelines will support the consortium to address the ammonia-specific set of safety and technology challenges.” More global ammonia developments In another development, three LPG/ammonia carrier ships have been ordered at the South Korean shipyard HD Hyundai Heavy Industries (HD HHI). Danish investment fund European Maritime Finance (EMF) and international shipping company Atlas Maritime have confirmed the order. HD HHI’s parent company, HD Korea Shipbuilding & Offshore Engineering (HD KSOE), revealed the order for $372 million in March 2024. The three 88,000 cubic-metre LPG dual-fuel carriers, capable of carrying and running on ammonia, are scheduled for delivery in December 2027. The vessels will be named EMF Viking I, II, and III. Also, Lloyd’s Register (LR) and Guangzhou Shipyard International have signed a joint development project to design the world’s largest very large ammonia carrier (VLAC). The design of the 100,000-cubic-metre vessel has been assessed in line with LR’s Structural Design Assessment and prescriptive analysis. The gas carrier will have an independent IMO Type B tank for safe carriage of the chemical. Zero-emissions operations The cargo ship, which will be 7,800 dwt, is designed to transport timber from Norway to Europe “As major economies look to co-fire ammonia in their coal power stations to reduce the CO2 footprint of their national energy mix, shipping will play a key role in distributing clean hydrogen-based commodities such as ammonia, thereby supporting nations to meet their Paris Agreement commitments," says LR's Chief Executive Nick Brown. Furthermore, a partnership of companies from Norway has ordered a pioneering short-sea cargo ship that will advance the industry’s ability to provide zero-emissions operations. The cargo ship, which will be 7,800 dwt, is designed to transport timber from Norway to Europe and will be the first to operate on ammonia and electricity. Amogy’s ammonia-to-electrical power system A start-up company focusing on ammonia-to-power technology, Amogy, demonstrated the first tugboat powered by its cracking technology just short of the fourth anniversary of the company’s launch. The trip of a 67-year-old tug along a tributary of New York State’s Hudson River is part of the company’s works to develop and commercialise its technology to decarbonise the most difficult industries. Amogy’s ammonia-to-electrical power system splits, or “cracks,” liquid ammonia into its base elements of hydrogen and nitrogen. The hydrogen is then funnelled into a fuel cell, generating the power for the vessel. Research points to the risks of ammonia The chemical, made of hydrogen and nitrogen, can also be burned as a zero-carbon fuel Today and in the future, ammonia, a main component of many fertilisers, can play a key role in a carbon-free fuel system as a convenient way to transport and store clean hydrogen. The chemical, made of hydrogen and nitrogen, can also be burned as a zero-carbon fuel. However, new research led by Princeton University scientists illustrates that even though it may not be a source of carbon pollution, ammonia's widespread use in the energy sector could pose a grave risk to the nitrogen cycle and climate without proper engineering precautions. Use of ammonia U.S. National Science Foundation (NSF)-supported research found that a mismanaged ammonia economy could ramp up emissions of nitrous oxide, a long-lived greenhouse gas around 300 times more potent than carbon dioxide and a major contributor to the thinning of the stratospheric ozone layer. The use of ammonia could lead to substantial emissions of nitrogen oxides, a class of pollutants that contribute to the formation of smog and acid rain. And it could directly leak fugitive ammonia emissions into the environment, forming air pollutants, impacting water quality and stressing ecosystems by disturbing the global nitrogen cycle. Negative impacts of an ammonia economy The researchers found that the potential negative impacts of an ammonia economy "We have great hope that ingenuity and engineering can help reduce our use of carbon-based energy sources," said Richard Yuretich, a program director in NSF's Division of Earth Sciences. "But caution is advised because of unintended environmental spillover effects that may result from new technology." The researchers found that the potential negative impacts of an ammonia economy may be minimised with proactive engineering practices, but the possibility of risks should not be taken lightly. Addressing an inconvenient reality As interest in hydrogen as a zero-carbon fuel has grown, so too has an inconvenient reality: It is notoriously difficult to store and transport over long distances, requiring storage at either temperatures below -253 degrees Celsius or at pressures as high as 700 times atmospheric pressure. Ammonia, on the other hand, is much easier to liquify, transport and store, and capable of being moved around similarly to tanks of propane. Nonetheless, the cycle of nitrogen is delicately balanced in Earth's critical zone, and extensive research must be undertaken to investigate the repercussions of ammonia combustion and to develop new methods to minimise the risks. Challenges of ammonia as a maritime fuel Here's a breakdown of the key challenges of using ammonia for maritime fuel: Toxicity and Safety: For human health, ammonia is highly toxic, posing a serious risk to human health through inhalation or skin contact. This necessitates stringent safety protocols, advanced leak detection systems, and thorough crew training. Relating to the environment, leaks can also harm aquatic ecosystems, requiring robust containment and mitigation measures. Combustion Challenges: Ammonia's combustion characteristics are less favourable than traditional fuels, requiring modifications to engine design and potentially the use of pilot fuels. Emissions: Combustion can produce nitrogen oxides (NOx) and nitrous oxide (N2O), both of which are harmful pollutants. Mitigating these emissions is crucial. "Ammonia slip" is also a concern, in which unburnt ammonia is released. Infrastructure and Supply Chain: Establishing a global network of ammonia bunkering infrastructure is a massive undertaking, requiring significant investment and coordination. Scaling up "green ammonia" production, using renewable energy, is essential for its sustainability. This requires a robust and reliable supply chain. Storage: Ammonia has specific storage requirements, and onboard storage systems must be designed for safety and efficiency. International Standards Needed: Consistent and comprehensive international regulations and standards are needed for the safe handling, transportation, and use of ammonia as a marine fuel. While the IMO is developing Guidelines, complete and ratified rules are still needed. Economic challenges: "Green ammonia" is currently more expensive than traditional fuels, although costs are expected to decrease as production scales up. Significant investments are needed in research, development, and infrastructure to make ammonia a viable maritime fuel. Also, dedicated ammonia-fueled engines are still under heavy development, and do not have widespread availability. The path to commercialisation Overcoming the variety of technical and other obstacles will require collaboration among governments, industry stakeholders, and research institutions. The timeline for ammonia deployment in maritime applications is actively unfolding, with key milestones happening now and soon. 2025 marks the first trials of two-stroke, ammonia dual-fuel engines on oceangoing ships. Engine manufacturers like MAN Energy Solutions and WinGD are progressing with their engine development, with initial deliveries soon. These pilot projects are crucial for gathering real-world data and building confidence in ammonia as a marine fuel. Development of comprehensive regulations As the maritime industry faces, ammonia is hoped to play a growing role in the fuel mix Gradual commercialisation will follow in the late-2020s as the technology matures and the infrastructure develops. The focus will be on refining engine technology, improving safety protocols, and establishing bunkering facilities in key ports. Wider adoption will likely follow in the 2030s, depending on factors such as the cost of green ammonia, the development of comprehensive regulations, and the expansion of the global supply chain. As the maritime industry faces increasing pressure to decarbonise, ammonia is expected to play a growing role in the fuel mix. Future of maritime It's likely that a combination of ammonia and other alternative fuels and technologies will be used in the future of maritime. Alternatives include methanol, liquid natural gas (LNG), hydrogen, biofuels, electric propulsion, and even nuclear power. Ammonia is a strong contender, bit it faces stiff competition from other promising technologies. The maritime industry's transition to a sustainable future will likely involve a diverse mix of fuel solutions.
The Dark Fleet refers to a network of vessels that operate outside of standard maritime regulations, often used to transport sanctioned goods such as oil. These shadowy vessels are also referred to by terms such as Parallel Fleet and/or Shadow, Gray or Ghost fleet. The terms are all manifestations of the same thing – ships that are owned, structured, and operated to avoid exposure to sanctions. Fleet of ships “In fact I would prefer that we use the term Parallel Fleet because it more accurately describes what it is,” says Mike Salthouse, Head of External Affairs, of NorthStandard, a Protection and Indemnity (P&I) insurer. “Specifically, it is a fleet of ships operating in parallel to mainstream shipping while avoiding use of service providers that are subject to sanctions legislation.” Modern shipping sanctions Sanctions were to be enforced not just against the sanctions-breaking vessel but also the services Modern shipping sanctions can be traced back to the introduction of the U.S. Comprehensive Iran Sanctions Accountability and Divestment Act 2010 or “CISADA”. Under CISADA for the first time, sanctions were to be enforced not just against the sanctions-breaking vessel but also the services (for example insurance, class, flag, banks) that the vessel used. EU/G7 Coalition adopting sanctions As a result, all maritime service providers sought to distance themselves and introduce contractual termination clauses in their service contracts forcing such vessels to either trade without such services or to access them from non-sanctioning jurisdictions. This led immediately to the creation of mainly Iranian ships that could continue to carry cargoes subject to western economic sanctions – such as Iranian oil. However, the fleet has grown exponentially following the EU/G7 Coalition adopting sanctions targeting Russian shipping. Today the majority (but not all) of the Dark Fleet is engaged carrying Russian cargoes – but other trades include Iran, North Korea, and Venezuela. Protection of the marine environment Dark Fleet undermines transparent governance policies that ensure the welfare and safety “It might be that a removal of Russian sanctions would remove the need for such a fleet,” adds Salthouse. “But for so long as nations use maritime sanctions as a foreign policy tool, my own view is that the Dark Fleet phenomenon will continue to facilitate sanctioned trades.” The Dark Fleet undermines transparent governance policies that ensure the welfare and safety of those on board and the protection of the marine environment. In recent years, the safety of tankers has improved significantly. These improvements have been driven by factors such as greater operational oversight from the oil majors, younger double hull vessels, greater operational scrutiny, and more rigorous legislation. Safety has been prioritised over all else. Transport oil using ships and services “The commercial dynamics that apply to the Dark Fleet are very different,” says Salthouse. “The overwhelming commercial imperative is not safety but to transport oil using ships and services to which sanctions legislation does not apply. As such, the customer and regulatory oversight is much reduced.” The vessels used by the Dark Fleet also tend to be older. Even if it were possible to find shipyards that were prepared to build for use carrying sanctioned cargoes (and so risk secondary sanctions depriving them of access to western financial markets and insurers), the long build times mean that such ships would not become available for several years. As such, the vessels that comprise the Dark Fleet tend to be end-of-life and aged 15 years or older. Commercial reinsurance markets The insurers of the ship will likely have been unable to access commercial reinsurance markets used If and when an accident happens, the ability of the insurer to respond by using commercial salvors and pollution responders will be curtailed by sanctions legislation, and the insurers of the ship will likely have been unable to access commercial reinsurance markets commonly used to access the high levels of cover required to fully compensate victims. Sanctioning individual ships is an effective way of addressing the Dark Fleet because shipping that trades internationally invariably needs access to western financial and service markets, which a designation deprives them of. Collaboration with mainstream shipping EU/G7 Coalition States to date have designated over 100 vessels, but in practical terms, the Dark Fleet is much larger than this – somewhere in the region 600 to 1000 vessels – so more needs to be done, says Salthouse. Thought also needs to be given as to how to dispose of old designated tonnage (as designation will prevent scrapping) whilst at the same time addressing the supply side so that designated ships cannot simply be replaced. “That can only be achieved in collaboration with mainstream shipping which should be consulted and partner with governments to achieve their aim,” says Salthouse. Majority of shipowners and service Dark Fleet will thrive for so long as maritime sanctions are deployed by states as a means of foreign policy goals Without concerted state action delving with the existing fleet and its access to new ships, the Dark Fleet will thrive for so long as maritime sanctions are deployed by states as a means of achieving their foreign policy goals. The cost of compliance to mainstream shipping is huge. The vast majority of shipowners and service providers deploy significant resources to avoid inadvertently contravening applicable sanctions. EU/G7 Coalition partners should recognise that and work with the shipping industry to marginalise the commercial space served by the Parallel/Dark Fleet rather than simply imposing ever greater and more complex compliance requirements, comments Salthouse. Use of EU/G7 Coalition service In a majority of cases, the Parallel Fleet is not breaking any laws. With the exception of the UN sanctions programme directed at North Korea, the Parallel/Dark Fleet can trade perfectly lawfully. For example, it is not illegal for a Russian flagged ship, insured in Russia, classed in Russia and trading with non-EU/G7 Coalition partners to transport Russian oil sold above the price cap through international waters to non-EU/G7 Coalition states provided the trade does not make use of EU/G7 Coalition service providers. Use of established service providers The Parallel/Dark Fleet is bad for shipping and undermines EU/G7, and on occasions, UN sanctions programmes, says Salthouse. States cannot control a trade when the ships carrying the cargoes and the service providers involved are not subject to the jurisdiction of that State. Similarly, when ships sink and cause pollution, the whole shipping industry suffers by association, and the additional complexities involved in responding to a casualty that cannot make use of established service providers could make a bad situation much worse.
Carbon capture and storage (CCS) can contribute to decarbonisation of the maritime industry, especially when combined with other approaches. CCS allows ships to continue using fossil fuels while capturing and storing the emitted CO2. It’s a helpful interim approach if a vessel’s immediate transition to alternative fuels is not feasible due to infrastructure limits or technology constraints. CCS can extend a vessel’s operational lifespan, both reducing emissions from existing vessels while avoiding premature scrapping and associated environmental impacts. Technology challenges There are technology challenges, such as higher fuel consumption and process costs for ships As the industry works toward the use of zero-emission fuels such as green hydrogen, ammonia and methanol, CCS offers a more gradual and realistic pathway to decarbonisation. CCS is also an attractive option for long-haul shipping routes where alternative fuel infrastructure may be limited. However, there are technology challenges, such as higher fuel consumption and operation costs for ships. Space constraints are another obstacle considering the needs to operate and install CCS equipment on board ships. Clear and supportive regulation More work is needed to provide secure and reliable long-term storage of captured CO2, which is still under development. Technology advancement and government incentives are also needed to increase the economic viability of Carbon Capture and Storage for ships operators. Clear and supportive regulation paves the way for widespread adoption of CCS in the maritime sector, including standards for capture, transport, and storage. Carbon capture and storage The amine solution, now loaded with CO2, is then sent to a regenerator (stripper) In a CCS system, carbon dioxide (CO2) is captured from a ship’s exhaust gases after the fuel has been burned. This often involves chemical absorption, in which the exhaust gases pass through a solvent that absorbs the CO2. A contactor (absorber) uses an amine solution to react chemically with the CO2, forming a carbamate compound. This effectively removes the CO2 from the flue gas. The amine solution, now loaded with CO2, is then sent to a regenerator (stripper). Heat is applied to the solution, causing the carbamate to decompose, releasing the captured CO2. Onshore storage sites The CO2 is then separated and stored onboard in high-pressure tanks as a liquid, and later offloaded at designated ports for transport to onshore storage sites. There is an energy penalty in the process, since CCS itself requires energy, which can increase fuel consumption and operating costs for the ship. Because onboard storage capacity for captured CO2 can be limited, frequent offloading is required. Adoption timeline for CCS Most CCS projects in the maritime sector are still in the research and development phase In the near term (5 to 10 years), initial deployments of CCS on select vessels will likely focus on niche applications or specific routes. Most CCS projects in the maritime sector are still in the research and development phase. Some pilot projects and demonstrations are underway to test the feasibility and effectiveness of CCS technologies, but large-scale commercial deployments of CCS systems on board ships are still to come. If technological advancements and economic viability improve, CCS could see more widespread adoption in the maritime sector within the next 10 to 20 years, particularly for vessels where alternative fuel options are limited or not yet feasible. The development of a robust infrastructure for the transport and storage of captured CO2 will be crucial for the large-scale deployment of CCS in the maritime. Requirements of CCS systems for maritime use Looking long-term (20 years or more), CCS could become a mature technology integrated into the broader maritime decarbonisation landscape, potentially playing a role alongside other technologies like alternative fuels and energy efficiency measures. Continued research and development will aim to improve the efficiency, cost-effectiveness, and space requirements of CCS systems for maritime use. The development of more efficient and compact CCS systems is crucial for their widespread adoption in the maritime sector. Reducing the costs, including capital expenditures and operational expenses, is also essential. Clear and supportive regulations, including carbon pricing mechanisms and incentives for CCS deployment, will encourage its adoption. Complementary technologies toward decarbonisation Another option is using fuel cells to convert hydrogen or other fuels into electricity for propulsion CCS can be used in conjunction with transitional fuels like Liquefied Natural Gas (LNG), capturing and storing CO2 emissions from LNG-powered vessels to reduce the carbon footprint while the industry transitions to zero-emission fuels. CCS can be particularly valuable for sectors where zero-emission alternatives may not be readily available or feasible, such as long-haul shipping. CCS can also serve as a backstop technology, providing a potential solution for residual emissions from alternative fuel pathways, even if they are considered low-carbon. A range of alternative fuel scenarios drive research and development into new technologies such as biofuels, green hydrogen, ammonia, and methanol. Another possibility is using fuel cells to convert hydrogen or other fuels into electricity for propulsion. Better battery technology, including better capacity and charging infrastructure, is needed. And ship designs must be optimised for alternative fuels, including storage and handling systems. Next stages for CCS The next stage in the development of carbon capture and storage (CCS) for maritime vessels will likely involve full-scale demonstration projects, moving beyond small-scale prototypes and lab tests to real-world applications on commercial vessels. More compact and lightweight systems will be developed to reduce the weight and space requirements on board ships. Viable business models and financial mechanisms are needed to make CCS economically attractive for ship owners. A clear and consistent regulatory framework can incentivise CCS adoption and ensure compliance with environmental standards. There also needs to be more public awareness and understanding of the role of CCS in decarbonising the maritime sector.
Case studies
Bennett Marine, a Division of Yamaha Marine Systems Company, needed a solution that integrated solar energy generation and mechanical upgrades to optimise both sustainability and working environment outcomes. However, adding the cooling capacity needed by a large warehouse, and the employees working there, during the long Floridian summers could significantly increase the utility load on the building. Solution Bennett Marine’s management approached its outsourced service provider, ABM. Having successfully completed two lighting upgrades on site, and acting as the current janitorial service provider, ABM took Bennet Marine’s request to its Infrastructure Solutions team. ABM’s Infrastructure Solutions designed an energy-efficient HVAC system supported by a rooftop solar PV array that offset utility costs with renewable energy, leading to a net 58% reduction in total utility usage for the building. ABM also assisted in securing tax credits and energy incentives for the project, as well as a new roof for the facility with additional building envelope improvements. Finding a better solution for the client ABM provides a consultative approach to help clients achieve sustainability goals, enable capital improvements" “Service experts across our company worked together to solve a need and deliver the sustainability solution Bennett Marine needed,” said Mark Hawkinson, President of ABM Technical Solutions. He adds, “ABM provides a consultative approach to help clients achieve sustainability goals, enable capital improvements, improve indoor air quality, address waste and inefficiency, and create a positive impact for communities.” In addition to the new roof, net energy offset, and improved cooling, ABM was able to assist the project in receiving an estimated $226,000 in tax credits and $224,000 in Energy Incentives through the Federal MACRS (Modified Accelerated Cost Recovery System). Benefits ABM’s Infrastructure Solutions enable businesses to invest in critical infrastructure needs and achieve sustainability, security, and resilience goals. A custom energy program drives costs out of operating budgets and redirects savings to critical needs, helping fund improvements. Highlights of the project for the Deerfield, Florida, warehouse include: Projected energy cost savings in the first year of $12,701 Replacement of ageing roof and speed roll doors to reduce energy loss Solar panel installation is capable of offsetting 66% of the building’s utility use
Korea Marine Transport Company Ship Management (KMTC SM) has reported annual fuel savings worth approximately US$540,000 in total after installing Accelleron’s digital engine optimisation solution Tekomar XPERT on 12 Panamax vessels. The fuel savings enabled KMTC SM to reduce its CO2 emissions by about 4,200 tons. Tekomar XPERT delivers engine optimisation recommendations based on thermodynamic insights that aim to bring engines back to the operating performance achieved at “new” conditions. The solution can be applied to any engine and turbocharger make. KMTC SM followed the advisory from Tekomar XPERT, tracked engine performance and benchmarked engines and vessels through Tekomar XPERT’s web portal (Loreka). Carbon Intensity Indicator (CII) ratings The reduced emissions will translate to better CII ratings and lower exposure to carbon pricing KMTC Ship Management General Manager of Environmental Technology, Jin-Seob Lee, said: “Based on the big savings on fuel cost and emission reduction, we aim to install Tekomar XPERT on our remaining 16 self-managed vessels, and will be recommending its installation on 22 other vessels managed by third parties.” Accelleron anticipates that KMTC’s fuel bill will be reduced by around US$1.3 million a year when Tekomar XPERT is deployed across all 50 vessels. The reduced emissions will translate to better Carbon Intensity Indicator (CII) ratings and lower exposure to carbon pricing, including the EU Emissions Trading System, which will apply to shipping from 2024. KMTC SM’s own measurements KMTC SM was able to track improvements in performance thanks to intuitive indicators and actionable insight from Tekomar XPERT. The reduced fuel consumption at the end of the 12-month period highlighted a significant increase in vessel performance over the year. This was verified by KMTC SM’s own measurements. Accelleron Global Head of Sales & Operations, Shailesh Shirsekar, said: “Efficient engines are one of the keys to reducing fuel costs, emissions and carbon price exposure, enabling optimisation without impact on vessel operation. With simple guidance from Tekomar XPERT, ship operators can ensure that the engines are running at their very best, laying the foundation for lower lifecycle costs as well as regulatory compliance.”
At Scheveningen Harbour in the coastal city of The Hague in the Netherlands, an AI-based video security system from Bosch Building Technologies is now ensuring that every single ship or boat entering or leaving the harbour is logged. The customised solution developed by Bosch together with its partner BrainCreators automatically registers and classifies shipping traffic. Intelligent security solution Until now, employees at the port control centre had to keep an eye on shipping traffic around the clock from the window of the control centre and manually record the 80 or so vessels that pass through the port every day. The city council of The Hague to quickly find a tailor-made solution for the port of Scheveningen The reason for the investment in the intelligent security solution was the fear that criminals would seek alternative routes via smaller ports such as Scheveningen, now that large Dutch or Belgian ports such as Rotterdam and Antwerp have been more secure against smuggled goods for some time. This was reason enough for the city council of The Hague to quickly find a tailor-made solution for the port of Scheveningen. Challenging task in Scheveningen Special conditions require individual solutions Most boats and ships entering the port of Scheveningen are not required to register and, unlike purely commercial ports such as Rotterdam, the port cannot simply be closed off. In addition to cargo ships, there are also fishing boats and private sailing yachts at anchor, with small dinghies and rowing boats cruising between them. Keeping track of the movement of goods in particular is therefore a challenging task in Scheveningen, where the video security system with intelligent video analysis installed by Bosch provides welcome support. Author's quote The requirements for this project were very specific because the shipping traffic not only had to be filmed" "The requirements for this project were very specific because the shipping traffic not only had to be filmed, but also registered and classified. The solution also had to provide information about the speed of travel," says Niels van Doorn, Senior Manager Solutions & Portfolio at Bosch Building Technologies in the Netherlands. "Standard software can't do that. Together with our partner, we have therefore developed an AI that can identify and classify ships of all kinds–from passenger ships and freighters to sailing yachts and inflatable boats." This data aids in identifying suspicious shipping movements. Flexidome IP starlight 8000i cameras No sooner said than done – and in the shortest possible time Development, planning and implementation only took around 12 months. Two intelligent video cameras at the mouth of the harbour now record the traffic. The specially developed AI classifies the ship types and registers them in a file. Due to the difficult lighting conditions in the port, the Flexidome IP starlight 8000i cameras from Bosch were chosen. They deliver detailed images even in challenging weather and lighting conditions and enable the staff in the control centre to see every detail, even in very bright or dark image sections. Ships that are not seen in real-time by the personnel on duty appear as still images on the screen All boat identifiers are recorded, documented, stored and automatically provided with additional information on date and time, direction of travel and speed around the clock using AI. The streams from the cameras are fed directly into a video management system. Ships that are not seen in real-time by the personnel on duty appear as still images on the screen. By analysing all the data, peak times, ship types, trends and deviations from the norm are determined. New video documentation "The dashboard gives staff an overview of all activities in the port. The software protects the privacy of the people recorded by making their faces unrecognisable. The new video documentation now provides solid evidence and helps to identify suspicious and unusual situations more quickly and effectively," says Ferry Ditewig, Business Development Manager at Bosch Building Technologies in the Netherlands. The video solution is also well equipped for future challenges and can be flexibly expanded as required: for example, additional information from external sources could be integrated, such as meteorological data, tides or the automatic identification system (AIS) for exchanging ship data.
San Francisco-based maritime technology company - Sofar Ocean announces a partnership with the U.S. Naval Meteorology and Oceanography Command’s (CNMOC) Fleet Weather centres in Norfolk (FWC-N) and San Diego (FWC-SD). Wayfinder platform FWC-N and FWC-SD, the Navy’s two primary weather forecasting centres, are piloting Sofar’s Wayfinder platform to support the routing of naval vessels at sea. The FWCs are utilising Wayfinder to identify safe and efficient route options powered by real-time ocean weather data for Military Sealift Command (MSC) ships. Situational awareness Tim Janssen, Co-Dounder and CEO of Sofar, said, "Wayfinder will empower the Navy to enhance situational awareness at sea and leverage data-driven optimisation to continuously identify safe and efficient routing strategies." He adds, "Powered by our real-time ocean weather sensor network, Wayfinder will help the Navy scale its routing operations to support a heterogeneous fleet operating in conditions made more extreme by the effects of climate change." CRADA The platform displays real-time observational data from Sofar’s global network of Spotter buoys The Navy is evaluating Wayfinder under CNMOC and Sofar’s five-year Cooperative Research and Development Agreement (CRADA) signed in July 2023. Wayfinder reduces manual tasks for forecasters and routers by automatically generating a forecast along a vessel’s route. The platform displays real-time observational data from Sofar’s global network of Spotter buoys to reduce weather uncertainty for route optimisation, and predict unwanted vessel motions during a voyage. Real-time wave and weather observations The availability of accurate real-time wave and weather observations helps Captains and shoreside personnel validate forecast models and examine multiple route options more efficiently, streamlining a historically complex and arduous process. Lea Locke-Wynn, Undersea Warfare Technical Lead for CNMOC’s Future Capabilities Department, said, "A key focus area for the Naval Oceanography enterprise is fostering a culture of innovation through collaboration with our commercial partners." Vessel-specific guidance Lea Locke-Wynn adds, "Our ongoing CRADA with Sofar Ocean is a perfect example of how our partnerships can leverage the leading edge in industry to further Department of Defence operations." As the number of naval vessels at sea, including experimental and autonomous ships, continues to increase, forecasters and routers will have less time to spend manually producing vessel-specific guidance. Automated forecast-on-route guidance More efficient routing empowers FWC personnel to focus on challenging, mission-critical tasks Wayfinder helps fill this operational gap, enabling FWC-N and FWC-SD to more efficiently support a large fleet in real-time with automated forecast-on-route guidance. More efficient routing empowers FWC personnel to focus on challenging, mission-critical tasks that require their unique expertise. Streamlined decisions Captain Erin Ceschini, Commanding Officer, FWC-SD, stated, "By using Wayfinder, we’re able to better visualise our ships’ routes, and make safer and more streamlined decisions on route, speed, and heading." Captain Erin Ceschini adds, "Wayfinder has the potential to be a critical component of our day-to-day operations and a key driver of safe routing as we contend with an increasingly unpredictable weather landscape."
The accuracy of AIS data used to track ship movements is vital for the analysis of vessel performance in areas such as fuel consumption. OrbitMI has therefore collaborated with Maritime Data on a joint project to enhance the screening of AIS data providers so it can deliver the best quality data for clients. Orbit vessel performance platform “We are continuously striving to optimise data inputs for users of our newly upgraded Orbit vessel performance platform to improve business decision-making." "With this goal in mind, we engaged Maritime Data as a trustworthy partner to contribute its specialist expertise in data procurement for the industry,” says OrbitMI’s Chief Marketing Officer David Levy. Assuring the quality of data inputs Maritime Data supports companies in the maritime ecosystem from concept to contract Maritime Data is a UK-based start-up founded in 2022 by Co-Founders Rory Proud and James Littlejohn with a mission to address the difficulties in sourcing, evaluating, and buying maritime data by acting as a specialised intermediary between buyer and supplier. As a data broker, Maritime Data supports companies in the maritime ecosystem from concept to contract. This enables clients to quickly understand all available solutions relevant to their requirements, evaluate comparable options, and contract with their suppliers of choice. All to minimise the effort required and give time back to the people building solutions needed to tackle the industry's biggest challenges. Buying data is made easier. Accurate customer service Backed by more than 15 years of experience in the sector, Maritime Data has built up an extensive partner network of over 50 maritime intelligence suppliers and 200-plus product offerings in areas such as vessel tracking, emissions calculation, seaborne cargo flows, risk and compliance, port activity, trade statistics, weather, and vessel ownership. “The quality of data being inputted into any model, process, or technology will have a meaningful impact on output,” explains Maritime Data’s Co-Founder James Littlejohn. "It is therefore essential for maritime technology companies to meaningfully evaluate all of their data inputs to ensure their solution provides the most accurate service for their customers." Tackling sourcing challenges Real-time data generated by the AIS is considered the X-axis for any evaluation of vessel operations The joint project has focused on tackling the challenges of acquiring the right AIS data arising from discrepancies in datasets offered by various vendors that make assessment and evaluation difficult for data buyers. Real-time data generated by the Automatic Identification System (AIS) is considered the X-axis for any evaluation of vessel operations and is a fundamental data layer for performance monitoring as it shows position, course, and speed, which can be combined with weather data to optimise operations, according to James Littlejohn. However, AIS is extremely data-heavy with hundreds of millions of data points being generated by thousands of vessels across the globe every day, which requires commensurately massive computational resources to ingest and analyse this data. New vendor evaluation protocol Under the joint project, Maritime Data conducted a comparative assessment of four leading AIS data providers using a new, specially developed evaluation protocol to ascertain the quality of their respective offerings based on carefully designed criteria. Maritime Data was able to take samples of a week of AIS data from each of the four providers and measure each dataset against various benchmarks provided by OrbitMI to help determine the coverage, accuracy and frequency of the respective feeds. A segment of these samples was then taken and split out over 80 different geolocations that were visualised as polygons on a map to show geographical coverage. Heavyweight analytics Independent validation of the supplier selection process enabled this to be conducted more quickly James Littlejohn points out that conducting this process of comparison and evaluation with such vast amounts of data would entail a lot of time and resources for a maritime technology firm such as OrbitMI, causing opportunity cost, while it took Maritime Data about a month to complete the analysis and this time is likely to be shortened in future as the process becomes more efficient. He says that independent validation of the supplier selection process enabled this to be conducted more quickly and without bias in favour of any one data vendor. “The outcome of the process was exactly as we expected and piloting this tool with OrbitMI has given us a springboard for further development and application of the selection protocol. This enabled OrbitMI to proceed with a decision on AIS sourcing secure in the knowledge that the data would fulfill the needs of its customers,” James Littlejohn says. Selecting the ideal AIS data provider At the end of the process, OrbitMI selected Lloyd's List Intelligence as its AIS data provider. “Lloyd's List Intelligence has been a long-time and valued partner of ours,” says Ali Riaz, OrbitMI's CEO. “The quality and versatility of their data offerings, assurances of data accuracy, customer service, and commitment to collaboration compared to the other offerings were unbeatable.” This decision aligns with Lloyd's List Intelligence's strategic vision for the industry. A collaborative, connected approach Tom Richmond, Head of Software & Technology Sales at Lloyd's List Intelligence, elaborates, “Working with innovators like OrbitMI is part of our strategic plan to help the shipping industry move beyond siloed thinking and kick-start a more collaborative, connected approach to integrating seaborne trade in the global supply chain." "We’re happy to support innovation with high-quality products at a price point that stimulates collaboration in the sector.” AIS data quality assurance OrbitMI’s David Levy concludes, “This project demonstrates we are prioritising data quality for our clients by harnessing the power of partnership with a major player." "The AIS data quality assurance process piloted by OrbitMI with Maritime Data will benefit users of the new Orbit platform by ensuring optimised and reliable data inputs covering the global fleet.”
Strengthening trade relations and promoting collaboration between Valenciaport and China. This is the objective with which the Port Authority of València has traveled to China to participate in the 8th edition of the Maritime Silk Road Port International Cooperation Forum 2024, held from June 26 to 28, 2024 in Ningbo (China). The value proposition of the Valencian enclosure as a green, intelligent and innovative HUB of the Mediterranean has been the common thread of the presentation of the PAV in this forum. Advantages of Valenciaport as a strategic port Mar Chao has also described the strategic importance of Valenciaport for the Chinese market During the event, Mar Chao, President of the PAV, had the opportunity to present the competitive advantages of Valenciaport as a strategic port in the center of the Mediterranean (through which 40% of Spanish import/export is channeled) at the service of the business fabric of its area of influence and a link in the logistics chain. Mar Chao has also described the strategic importance of Valenciaport for the Chinese market as a key point of direct connection with Europe that promotes a green growth, market-oriented, with maximum efficiency in services and a complete logistic and multimodal integration. Commercial capacity of Valenciaport During her conference, the President also highlighted the commercial capacity of Valenciaport, with an area of influence of more than 2,000 kilometres that maintains a direct relationship with the main international ports. Cristina Rodríguez, Head of Containers of Valenciaport, accompanies Chao in the forum. Both have held business meetings with Asian companies and institutions, including the new president of the Port of Ningbo, Tao Chengbo. In the framework of this meeting, the representatives of Valenciaport and the Port of Ningbo have signed a memorandum of understanding (MOU) with the aim of strengthening their commercial collaboration. Silk Road Port and Maritime Cooperation Forum The Silk Road Port and Maritime Cooperation Forum of Ningbo (China) in which Valenciaport participates is a platform for open exchange and mutual learning in port development and maritime transport, within the framework of the Belt and Road Initiative. From a respect for the uniqueness of each participating port, the Forum is seen as a tool to foster collaboration in various fields to build bridges between supply and demand in business, investment, technology, talent, information, ports and cultural exchange.
Bennett Marine, a Division of Yamaha Marine Systems Company, needed a solution that integrated solar energy generation and mechanical upgrades to optimise both sustainability and working environment outcomes. However, adding the cooling capacity needed by a large warehouse, and the employees working there, during the long Floridian summers could significantly increase the utility load on the building. Solution Bennett Marine’s management approached its outsourced service provider, ABM. Having successfully completed two lighting upgrades on site, and acting as the current janitorial service provider, ABM took Bennet Marine’s request to its Infrastructure Solutions team. ABM’s Infrastructure Solutions designed an energy-efficient HVAC system supported by a rooftop solar PV array that offset utility costs with renewable energy, leading to a net 58% reduction in total utility usage for the building. ABM also assisted in securing tax credits and energy incentives for the project, as well as a new roof for the facility with additional building envelope improvements. Finding a better solution for the client ABM provides a consultative approach to help clients achieve sustainability goals, enable capital improvements" “Service experts across our company worked together to solve a need and deliver the sustainability solution Bennett Marine needed,” said Mark Hawkinson, President of ABM Technical Solutions. He adds, “ABM provides a consultative approach to help clients achieve sustainability goals, enable capital improvements, improve indoor air quality, address waste and inefficiency, and create a positive impact for communities.” In addition to the new roof, net energy offset, and improved cooling, ABM was able to assist the project in receiving an estimated $226,000 in tax credits and $224,000 in Energy Incentives through the Federal MACRS (Modified Accelerated Cost Recovery System). Benefits ABM’s Infrastructure Solutions enable businesses to invest in critical infrastructure needs and achieve sustainability, security, and resilience goals. A custom energy program drives costs out of operating budgets and redirects savings to critical needs, helping fund improvements. Highlights of the project for the Deerfield, Florida, warehouse include: Projected energy cost savings in the first year of $12,701 Replacement of ageing roof and speed roll doors to reduce energy loss Solar panel installation is capable of offsetting 66% of the building’s utility use
Korea Marine Transport Company Ship Management (KMTC SM) has reported annual fuel savings worth approximately US$540,000 in total after installing Accelleron’s digital engine optimisation solution Tekomar XPERT on 12 Panamax vessels. The fuel savings enabled KMTC SM to reduce its CO2 emissions by about 4,200 tons. Tekomar XPERT delivers engine optimisation recommendations based on thermodynamic insights that aim to bring engines back to the operating performance achieved at “new” conditions. The solution can be applied to any engine and turbocharger make. KMTC SM followed the advisory from Tekomar XPERT, tracked engine performance and benchmarked engines and vessels through Tekomar XPERT’s web portal (Loreka). Carbon Intensity Indicator (CII) ratings The reduced emissions will translate to better CII ratings and lower exposure to carbon pricing KMTC Ship Management General Manager of Environmental Technology, Jin-Seob Lee, said: “Based on the big savings on fuel cost and emission reduction, we aim to install Tekomar XPERT on our remaining 16 self-managed vessels, and will be recommending its installation on 22 other vessels managed by third parties.” Accelleron anticipates that KMTC’s fuel bill will be reduced by around US$1.3 million a year when Tekomar XPERT is deployed across all 50 vessels. The reduced emissions will translate to better Carbon Intensity Indicator (CII) ratings and lower exposure to carbon pricing, including the EU Emissions Trading System, which will apply to shipping from 2024. KMTC SM’s own measurements KMTC SM was able to track improvements in performance thanks to intuitive indicators and actionable insight from Tekomar XPERT. The reduced fuel consumption at the end of the 12-month period highlighted a significant increase in vessel performance over the year. This was verified by KMTC SM’s own measurements. Accelleron Global Head of Sales & Operations, Shailesh Shirsekar, said: “Efficient engines are one of the keys to reducing fuel costs, emissions and carbon price exposure, enabling optimisation without impact on vessel operation. With simple guidance from Tekomar XPERT, ship operators can ensure that the engines are running at their very best, laying the foundation for lower lifecycle costs as well as regulatory compliance.”
At Scheveningen Harbour in the coastal city of The Hague in the Netherlands, an AI-based video security system from Bosch Building Technologies is now ensuring that every single ship or boat entering or leaving the harbour is logged. The customised solution developed by Bosch together with its partner BrainCreators automatically registers and classifies shipping traffic. Intelligent security solution Until now, employees at the port control centre had to keep an eye on shipping traffic around the clock from the window of the control centre and manually record the 80 or so vessels that pass through the port every day. The city council of The Hague to quickly find a tailor-made solution for the port of Scheveningen The reason for the investment in the intelligent security solution was the fear that criminals would seek alternative routes via smaller ports such as Scheveningen, now that large Dutch or Belgian ports such as Rotterdam and Antwerp have been more secure against smuggled goods for some time. This was reason enough for the city council of The Hague to quickly find a tailor-made solution for the port of Scheveningen. Challenging task in Scheveningen Special conditions require individual solutions Most boats and ships entering the port of Scheveningen are not required to register and, unlike purely commercial ports such as Rotterdam, the port cannot simply be closed off. In addition to cargo ships, there are also fishing boats and private sailing yachts at anchor, with small dinghies and rowing boats cruising between them. Keeping track of the movement of goods in particular is therefore a challenging task in Scheveningen, where the video security system with intelligent video analysis installed by Bosch provides welcome support. Author's quote The requirements for this project were very specific because the shipping traffic not only had to be filmed" "The requirements for this project were very specific because the shipping traffic not only had to be filmed, but also registered and classified. The solution also had to provide information about the speed of travel," says Niels van Doorn, Senior Manager Solutions & Portfolio at Bosch Building Technologies in the Netherlands. "Standard software can't do that. Together with our partner, we have therefore developed an AI that can identify and classify ships of all kinds–from passenger ships and freighters to sailing yachts and inflatable boats." This data aids in identifying suspicious shipping movements. Flexidome IP starlight 8000i cameras No sooner said than done – and in the shortest possible time Development, planning and implementation only took around 12 months. Two intelligent video cameras at the mouth of the harbour now record the traffic. The specially developed AI classifies the ship types and registers them in a file. Due to the difficult lighting conditions in the port, the Flexidome IP starlight 8000i cameras from Bosch were chosen. They deliver detailed images even in challenging weather and lighting conditions and enable the staff in the control centre to see every detail, even in very bright or dark image sections. Ships that are not seen in real-time by the personnel on duty appear as still images on the screen All boat identifiers are recorded, documented, stored and automatically provided with additional information on date and time, direction of travel and speed around the clock using AI. The streams from the cameras are fed directly into a video management system. Ships that are not seen in real-time by the personnel on duty appear as still images on the screen. By analysing all the data, peak times, ship types, trends and deviations from the norm are determined. New video documentation "The dashboard gives staff an overview of all activities in the port. The software protects the privacy of the people recorded by making their faces unrecognisable. The new video documentation now provides solid evidence and helps to identify suspicious and unusual situations more quickly and effectively," says Ferry Ditewig, Business Development Manager at Bosch Building Technologies in the Netherlands. The video solution is also well equipped for future challenges and can be flexibly expanded as required: for example, additional information from external sources could be integrated, such as meteorological data, tides or the automatic identification system (AIS) for exchanging ship data.
San Francisco-based maritime technology company - Sofar Ocean announces a partnership with the U.S. Naval Meteorology and Oceanography Command’s (CNMOC) Fleet Weather centres in Norfolk (FWC-N) and San Diego (FWC-SD). Wayfinder platform FWC-N and FWC-SD, the Navy’s two primary weather forecasting centres, are piloting Sofar’s Wayfinder platform to support the routing of naval vessels at sea. The FWCs are utilising Wayfinder to identify safe and efficient route options powered by real-time ocean weather data for Military Sealift Command (MSC) ships. Situational awareness Tim Janssen, Co-Dounder and CEO of Sofar, said, "Wayfinder will empower the Navy to enhance situational awareness at sea and leverage data-driven optimisation to continuously identify safe and efficient routing strategies." He adds, "Powered by our real-time ocean weather sensor network, Wayfinder will help the Navy scale its routing operations to support a heterogeneous fleet operating in conditions made more extreme by the effects of climate change." CRADA The platform displays real-time observational data from Sofar’s global network of Spotter buoys The Navy is evaluating Wayfinder under CNMOC and Sofar’s five-year Cooperative Research and Development Agreement (CRADA) signed in July 2023. Wayfinder reduces manual tasks for forecasters and routers by automatically generating a forecast along a vessel’s route. The platform displays real-time observational data from Sofar’s global network of Spotter buoys to reduce weather uncertainty for route optimisation, and predict unwanted vessel motions during a voyage. Real-time wave and weather observations The availability of accurate real-time wave and weather observations helps Captains and shoreside personnel validate forecast models and examine multiple route options more efficiently, streamlining a historically complex and arduous process. Lea Locke-Wynn, Undersea Warfare Technical Lead for CNMOC’s Future Capabilities Department, said, "A key focus area for the Naval Oceanography enterprise is fostering a culture of innovation through collaboration with our commercial partners." Vessel-specific guidance Lea Locke-Wynn adds, "Our ongoing CRADA with Sofar Ocean is a perfect example of how our partnerships can leverage the leading edge in industry to further Department of Defence operations." As the number of naval vessels at sea, including experimental and autonomous ships, continues to increase, forecasters and routers will have less time to spend manually producing vessel-specific guidance. Automated forecast-on-route guidance More efficient routing empowers FWC personnel to focus on challenging, mission-critical tasks Wayfinder helps fill this operational gap, enabling FWC-N and FWC-SD to more efficiently support a large fleet in real-time with automated forecast-on-route guidance. More efficient routing empowers FWC personnel to focus on challenging, mission-critical tasks that require their unique expertise. Streamlined decisions Captain Erin Ceschini, Commanding Officer, FWC-SD, stated, "By using Wayfinder, we’re able to better visualise our ships’ routes, and make safer and more streamlined decisions on route, speed, and heading." Captain Erin Ceschini adds, "Wayfinder has the potential to be a critical component of our day-to-day operations and a key driver of safe routing as we contend with an increasingly unpredictable weather landscape."
The accuracy of AIS data used to track ship movements is vital for the analysis of vessel performance in areas such as fuel consumption. OrbitMI has therefore collaborated with Maritime Data on a joint project to enhance the screening of AIS data providers so it can deliver the best quality data for clients. Orbit vessel performance platform “We are continuously striving to optimise data inputs for users of our newly upgraded Orbit vessel performance platform to improve business decision-making." "With this goal in mind, we engaged Maritime Data as a trustworthy partner to contribute its specialist expertise in data procurement for the industry,” says OrbitMI’s Chief Marketing Officer David Levy. Assuring the quality of data inputs Maritime Data supports companies in the maritime ecosystem from concept to contract Maritime Data is a UK-based start-up founded in 2022 by Co-Founders Rory Proud and James Littlejohn with a mission to address the difficulties in sourcing, evaluating, and buying maritime data by acting as a specialised intermediary between buyer and supplier. As a data broker, Maritime Data supports companies in the maritime ecosystem from concept to contract. This enables clients to quickly understand all available solutions relevant to their requirements, evaluate comparable options, and contract with their suppliers of choice. All to minimise the effort required and give time back to the people building solutions needed to tackle the industry's biggest challenges. Buying data is made easier. Accurate customer service Backed by more than 15 years of experience in the sector, Maritime Data has built up an extensive partner network of over 50 maritime intelligence suppliers and 200-plus product offerings in areas such as vessel tracking, emissions calculation, seaborne cargo flows, risk and compliance, port activity, trade statistics, weather, and vessel ownership. “The quality of data being inputted into any model, process, or technology will have a meaningful impact on output,” explains Maritime Data’s Co-Founder James Littlejohn. "It is therefore essential for maritime technology companies to meaningfully evaluate all of their data inputs to ensure their solution provides the most accurate service for their customers." Tackling sourcing challenges Real-time data generated by the AIS is considered the X-axis for any evaluation of vessel operations The joint project has focused on tackling the challenges of acquiring the right AIS data arising from discrepancies in datasets offered by various vendors that make assessment and evaluation difficult for data buyers. Real-time data generated by the Automatic Identification System (AIS) is considered the X-axis for any evaluation of vessel operations and is a fundamental data layer for performance monitoring as it shows position, course, and speed, which can be combined with weather data to optimise operations, according to James Littlejohn. However, AIS is extremely data-heavy with hundreds of millions of data points being generated by thousands of vessels across the globe every day, which requires commensurately massive computational resources to ingest and analyse this data. New vendor evaluation protocol Under the joint project, Maritime Data conducted a comparative assessment of four leading AIS data providers using a new, specially developed evaluation protocol to ascertain the quality of their respective offerings based on carefully designed criteria. Maritime Data was able to take samples of a week of AIS data from each of the four providers and measure each dataset against various benchmarks provided by OrbitMI to help determine the coverage, accuracy and frequency of the respective feeds. A segment of these samples was then taken and split out over 80 different geolocations that were visualised as polygons on a map to show geographical coverage. Heavyweight analytics Independent validation of the supplier selection process enabled this to be conducted more quickly James Littlejohn points out that conducting this process of comparison and evaluation with such vast amounts of data would entail a lot of time and resources for a maritime technology firm such as OrbitMI, causing opportunity cost, while it took Maritime Data about a month to complete the analysis and this time is likely to be shortened in future as the process becomes more efficient. He says that independent validation of the supplier selection process enabled this to be conducted more quickly and without bias in favour of any one data vendor. “The outcome of the process was exactly as we expected and piloting this tool with OrbitMI has given us a springboard for further development and application of the selection protocol. This enabled OrbitMI to proceed with a decision on AIS sourcing secure in the knowledge that the data would fulfill the needs of its customers,” James Littlejohn says. Selecting the ideal AIS data provider At the end of the process, OrbitMI selected Lloyd's List Intelligence as its AIS data provider. “Lloyd's List Intelligence has been a long-time and valued partner of ours,” says Ali Riaz, OrbitMI's CEO. “The quality and versatility of their data offerings, assurances of data accuracy, customer service, and commitment to collaboration compared to the other offerings were unbeatable.” This decision aligns with Lloyd's List Intelligence's strategic vision for the industry. A collaborative, connected approach Tom Richmond, Head of Software & Technology Sales at Lloyd's List Intelligence, elaborates, “Working with innovators like OrbitMI is part of our strategic plan to help the shipping industry move beyond siloed thinking and kick-start a more collaborative, connected approach to integrating seaborne trade in the global supply chain." "We’re happy to support innovation with high-quality products at a price point that stimulates collaboration in the sector.” AIS data quality assurance OrbitMI’s David Levy concludes, “This project demonstrates we are prioritising data quality for our clients by harnessing the power of partnership with a major player." "The AIS data quality assurance process piloted by OrbitMI with Maritime Data will benefit users of the new Orbit platform by ensuring optimised and reliable data inputs covering the global fleet.”
Strengthening trade relations and promoting collaboration between Valenciaport and China. This is the objective with which the Port Authority of València has traveled to China to participate in the 8th edition of the Maritime Silk Road Port International Cooperation Forum 2024, held from June 26 to 28, 2024 in Ningbo (China). The value proposition of the Valencian enclosure as a green, intelligent and innovative HUB of the Mediterranean has been the common thread of the presentation of the PAV in this forum. Advantages of Valenciaport as a strategic port Mar Chao has also described the strategic importance of Valenciaport for the Chinese market During the event, Mar Chao, President of the PAV, had the opportunity to present the competitive advantages of Valenciaport as a strategic port in the center of the Mediterranean (through which 40% of Spanish import/export is channeled) at the service of the business fabric of its area of influence and a link in the logistics chain. Mar Chao has also described the strategic importance of Valenciaport for the Chinese market as a key point of direct connection with Europe that promotes a green growth, market-oriented, with maximum efficiency in services and a complete logistic and multimodal integration. Commercial capacity of Valenciaport During her conference, the President also highlighted the commercial capacity of Valenciaport, with an area of influence of more than 2,000 kilometres that maintains a direct relationship with the main international ports. Cristina Rodríguez, Head of Containers of Valenciaport, accompanies Chao in the forum. Both have held business meetings with Asian companies and institutions, including the new president of the Port of Ningbo, Tao Chengbo. In the framework of this meeting, the representatives of Valenciaport and the Port of Ningbo have signed a memorandum of understanding (MOU) with the aim of strengthening their commercial collaboration. Silk Road Port and Maritime Cooperation Forum The Silk Road Port and Maritime Cooperation Forum of Ningbo (China) in which Valenciaport participates is a platform for open exchange and mutual learning in port development and maritime transport, within the framework of the Belt and Road Initiative. From a respect for the uniqueness of each participating port, the Forum is seen as a tool to foster collaboration in various fields to build bridges between supply and demand in business, investment, technology, talent, information, ports and cultural exchange.


Round table discussion
More than almost any trend, decarbonisation is driving the future of maritime. That reality alone makes decarbonisation the perfect topic for our first-ever Expert Panel Roundtable column. Traditional maritime fuels, like heavy fuel oil, release harmful pollutants that contribute to air pollution and have adverse health effects. We have to do better, and discussions in the maritime industry centre on which combination of alternative fuels and other technologies can solve the shorter- and longer-term challenges of decarbonisation. For an update on the various approaches, we asked our Expert Panel Roundtable: What are the latest maritime technology trends in decarbonisation?